Parametric optimization for hardness of tig welded duplex stainless steel
DOI:
https://doi.org/10.12928/ijio.v4i2.7756Keywords:
Annova, Duplex stainless steel, Hardness, Optimization, Tungsten inert gas weldingAbstract
Achieving optimal mechanical properties in welding joints hinges on employing precise parametric conditions. This is particularly crucial for Tungsten Inert Gas (TIG) welding of ASTM/UNS 2205 Duplex Stainless Steel (DSS), where attributes like hardness, ultimate tensile strength, and yield strength are paramount. Maintaining high Hardness Value (HV) demands proper welding parameters such as welding current, gas flow rate, and welding speed. To enhance DSS welding quality, especially hardness, this study utilizes the Taguchi method to optimize welding process parameters. The importance of each factor is assessed through Annova statistical analysis. The outcomes highlight the positive impact of parametric optimization on HV, as evidenced by the analysed data. Parametric optimization proves to be a potent approach for refining industrial processes like welding, with particular relevance in TIG welding of duplex stainless steel due to its mechanical robustness and corrosion resistance. Nevertheless, challenges arise due to the material's elevated hardness and low thermal conductivity, resulting in potential defects like cracks and porosity. The identification of optimal welding parameters, encompassing current, voltage, speed, and gas flow rate, helps address these challenges and advances high-quality welds. Through systematic variations and analysis of these parameters, researchers and engineers can pinpoint the optimal combination that mitigates defects while maximizing desired joint attributes. Within the realm of TIG welding of duplex stainless steel, metric optimization holds the potential to elevate welding quality, curtail costs and waste, and heighten productivity and safety. Consequently, organizations can attain enhanced performance, efficiency, and profitability within their welding processes
References
N. Murugan, R. S. Parmar, and S. K. Sud, "Effect of submerged arc process variables on dilution and bead geometry in single wire surfacing," J. Mater. Process. Technol., vol. 37, pp. 767-780, 1993, doi: https://doi.org/10.1016/0924-0136(93)90135-S
R. Badji, M. Bouabdallah, B. Bacroix, C. Kahloun, B. Belkessa, and H. Maza, "Phase transformation and mechanical behavior in annealed 2205 duplex stainless steel welds," Mater. Charact., vol. 59, pp. 447-453, 2008. doi: https://doi.org/10.1016/j.matchar.2007.06.014.
M. E. Sotomayor, J. Sanz, A. Cervera, B. Levenfeld, and A. Várez, "Surface modification of a duplex stainless steel for plastic-metal hybrid parts," Arch. Mater. Sci. Eng., vol. 72, pp. 86-93, 2015. doi: https://doi.org/10.5604/12303666.1141376.
P. K. Palani and N. Murugan, "Sensitivity Analysis for Process Parameters in Cladding of Stainless Steel by Flux Cored Arc Welding," J. Manuf. Process., vol. 8, pp. 90-100, 2006. doi: https://doi.org/10.1016/j.jmapro.2006.09.001.
J. J. Del Coz Diaz, P. M. Rodriguez, P. J. G. Nieto, and D. Castro-Fresno, "Comparative analysis of TIG welding distortions between austenitic and duplex stainless steels by FEM," J. Appl. Thermal Eng., vol. 30, pp. 2448-2459, 2010. doi: https://doi.org/10.1016/j.applthermaleng.2010.05.008.
S. N. Pandya and J. V. Menghani, "Developments of mathematical models for prediction of tensile properties of dissimilar AA6061-T6 to Cu welds prepared by friction stir welding process using Zn interlayer," Sadhana, vol. 43, pp. 1-18, 2018. doi: https://doi.org/10.1007/s12046-018-0779-4.
Y. S. Tarng and W. H. Yang, "Optimisation of the weld bead geometry in gas tungsten arc welding by the Taguchi method," Int. J. Adv. Manuf. Technol., vol. 14, pp. 549-554, 1998. doi: https://doi.org/10.1007/s001700050108.
Y. S. Tarng, W. H. Yang, and S. C. Juang, "The use of fuzzy logic in the Taguchi method for the optimisation of the submerged arc welding process," Int. J. Adv. Manuf. Technol., vol. 16, pp. 688-694, 2000. doi: https://doi.org/10.1007/s001700070006.
Y. S. Tarng, S. C. Juang, and C. H. Chang, "The use of grey-based Taguchi methods to determine submerged arc welding process parameters in hard facing," J. Mater. Process. Technol.,vol.128, pp. 1-6, 2002 doi: https://doi.org/10.1016/S0924-0136(02)00395-5.
R. H. Murta, F. D. Braga, P. P. Maia, O. B. Diogenes, and E. P. De Moura, "Mathematical modeling for predicting mechanical properties in rebar manufacturing," Ironmaking Steelmaking, vol. 48, pp. 161-169, 2021. doi: https://doi.org/10.1080/03019233.2020.1853244.
R. Badjia, B. Bacroix, and M. Bouabdallah, "Texture, microstructure and anisotropic properties in annealed 2205 duplex stainless steel welds," J. Mater. Charact., vol. 62, pp. 833-843, 2011. doi: https://doi.org/10.1016/j.matchar.2011.06.011.
Ul-Haq, H. Weiland, and J. H. Bunge, "Textures and microstructures in duplex stainless steel," Mater. Sci. Technol., vol. 10, pp. 289-298, 1994. doi: https://doi.org/10.1179/mst.1994.10.4.289.
V. Barabash et al., "Materials challenges for ITER – current status and future activities," J. Nucl. Mater., vol. 367-370, 2007. doi: https://doi.org/10.1016/j.jnucmat.2007.04.023.
K. Ioki et al., "Design improvement and R&D achievements for VV and in vessel components towards ITER construction," Nucl. Fusion, vol. 43, pp. 268-273, 2003. doi: https://doi.org/10.1088/0029-5515/43/3/005.
A. Sanderson, C. S. Punshon, and J. D. Russell, "Advanced welding processes for fusion reactor fabrication," Fusion Eng. Des., vol. 49-50, pp. 77-87, 2000. doi: https://doi.org/10.1016/S0920-3796(00)00298-0.
G. Kalinin et al., "ITER R&D: vacuum vessel and in-vessel components: materials development and test," Fusion Eng. Des., vol. 55, pp. 231-246, 2001. doi: https://doi.org/10.1016/S0920-3796(00)00329-2.
L. P. Jones et al., "Towards advanced welding methods for the ITER vacuum vessel sectors," Fusion Eng. Des., vol. 69, pp. 215-220, 2003. doi: https://doi.org/10.1016/S0920-3796(03)00262-5.
M. Ozonuka et al., "Manufacturing and maintenance technologies developed for a thick wall structure of ITER vacuum vessel," Fusion Eng. Des., vol. 55, pp. 397-410, 2001. doi: https://doi.org/10.1016/S0920-3796(00)00348-6.
K. Shimizu et al., "Demonstration tests for manufacturing the ITER vacuum vessel," Fusion Eng. Des., vol. 82, pp. 2081-2088, 2007. doi: 10.1016/j.fusengdes.2007.02.096.
W. Chung et al., "Fabrication of a full-scale mock-up for inboard 10° section of ITER vacuum vessel thermal shield," Fusion Eng. Des., vol. 86, pp. 1928-1932, 2011. doi: https://doi.org/10.1016/j.fusengdes.2011.03.055.
M. Nakahira, N. Takeda, S. Kakudate, and M. Onozuka, "A proposal of ITER vacuum vessel fabrication specification and results of the full-scale partial mock-up test," Fusion Eng. Des., vol. 83, pp. 1578-1582, 2008. doi: https://doi.org/10.1016/j.fusengdes.2008.06.024.
O. I. Tobechukwu, C. E. Chinwuko, C. E. Mgbemena, and C. O. Chinedum Ogonna Mgbemena, "Gas lift optimization in the oil and gas production process: a review of production challenges and optimization strategies," Int. J. Ind. Optim., vol. 1, no.2, p. 61, 2020, doi: https://doi.org/10.12928/ijio.v1i2.2470
A. Parkhan and M. R. A. Purnomo, "Quality by design of yogurt product using Taguchi multi-responses method," Int. J. Ind. Optim., vol. 1, no.2, p. 81, 2020, doi: https://doi.org/10.12928/ijio.v1i2.2442
M. P. Mishra, H. U. Borgstedt, M. D. Mathew, S. L. Mannan, P. Rodriguez, et al., “A comparative study of creep rupture behaviour of modified 316L (N) base metal and 316L (N) 16-8-2 weldment in air and liquid sodium environments.”, Int. J. Press. Vessels Pip., vol. 72, pp. 111-118, 1997, doi: https://doi.org/10.1016/S0308-0161(97)00016-1
M. Vasudevan, A.K. Bhaduri, and B. Raj, Microstructure and Mechanical Properties of Austenitic Stainless Steels, International Welding Congress, February 16 – 19, 2005 Mumbai
C. R. Heiple, "Mechanism for minor element effect on GTA fusion zone geometry," Welding Journal, vol. 61, pp. 97s-102s, 1982. Available online: https://app.aws.org/wj/supplement/WJ_1982_04_s97.pdf
K. C. Mills and B. J. Keene, "Factors affecting variable weld penetration," Int. Mater. Rev., vol. 35, no. 1, pp. 185-216, 1990, doi: https://doi.org/10.1179/095066090790323966
Anderson, P.C.J., and Wiktorowicz, R., (1995), A-TIG welding – The effect of the shielding gas, TWI Bulletin, July/August, p. 76-77.
P. C. J. Anderson and R. Wiktorowicz, "Improving productivity with A-TIG welding," Welding and metal fabrication, vol. 64, no. 3, pp. 108-109, 1996.
B. Lucas, "Activating flux- improving the performance of the TIG process," Welding and Metal Fabrication, vol. 68, no. 2, pp. 7-10, 2000. Available online: https://www.twi-global.com/technical-knowledge/published-papers/activating-flux-improving-the-performance-of-the-tig-process-february-2000
W. Lucas, "Activating flux increasing the performance and productivity of the TIG and plasma process," Welding and Metal fabrication, pp. 11-17, 1996. Available: https://cir.nii.ac.jp/crid/1570291224515389568
T. Paskell, C. Lundin, and H. Castner, "GTAW flux increases weld joint penetration," Welding Journal, vol. 76, no. 4, pp. 57-62, 1997. Available: https://pascal-francis.inist.fr/vibad/index.php?action=getRecordDetail&idt=2621460
M. Tanaka, T. Shimizu et al., "Effects of activating flux on arc phenomena in gas tungsten arc welding," Sci. Technol. Weld. Join., vol. 5, no. 6, pp. 397-402, 2000, doi: https://doi.org/10.1179/136217100101538461
M. Vasudevan, "Computational and experimental studies on arc welded austenitic stainless steels," PhD thesis, Indian Institute of Technology, Madras, India, 2007.
V. Muthukumaran, A. K. Bhaduri, and B. Raj, "U.S. Patent No. 8,097,826," 2012.
M. Vasudevan, A. K. Bhaduri, and B. Raj, "Development and Evaluation of Activated Flux for TIG Welding of Type 304LN and Type 316LN Stainless Steels," Proc. of the Inter. Institute of Welding, International Congress, Chennai, 2008.
K. A. Yushchenko, A. A. Nakonechnyi, Y. G. Vysotskii, L. B. Kuznetsov, & L.B. Alekseev. Welding strips of copper alloys alloyed with beryllium. Welding international, 7(2), 134-137. 1993, doi: https://doi.org/10.1080/09507119309548358
P. Palanichamy, M. Vasudevan, and T. Jayakumar, "Measurement of residual stresses in austenitic stainless steel weld joints using ultrasonic technique," Sci. Technol. Weld. Join., vol. 14, no. 2, pp. 166-171, 2009, doi: https://doi.org/10.1179/136217108X394753
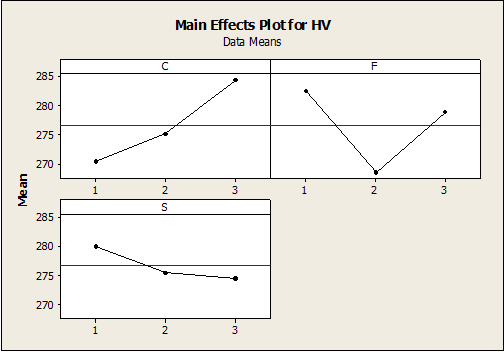
Downloads
Published
How to Cite
Issue
Section
License
Copyright (c) 2023 Sandip Mondal, Goutam Kumar Bose

This work is licensed under a Creative Commons Attribution-ShareAlike 4.0 International License.
License and Copyright Agreement
In submitting the manuscript to the journal, the authors certify that:
- They are authorized by their co-authors to enter into these arrangements.
- The work described has not been formally published before, except in the form of an abstract or as part of a published lecture, review, thesis, or overlay journal. Please also carefully read the International Journal of Industrial Optimization (IJIO) Author Guidelines at http://journal2.uad.ac.id/index.php/ijio/about/submissions#onlineSubmissions
- That it is not under consideration for publication elsewhere,
- That its publication has been approved by all the author(s) and by the responsible authorities tacitly or explicitly of the institutes where the work has been carried out.
- They secure the right to reproduce any material that has already been published or copyrighted elsewhere.
- They agree to the following license and copyright agreement.
Copyright
Authors who publish with the International Journal of Industrial Optimization (IJIO) agree to the following terms:
- Authors retain copyright and grant the journal right of first publication with the work simultaneously licensed under a Creative Commons Attribution License (CC BY-SA 4.0) that allows others to share the work with an acknowledgment of the work's authorship and initial publication in this journal.
- Authors are able to enter into separate, additional contractual arrangements for the non-exclusive distribution of the journal's published version of the work (e.g., post it to an institutional repository or publish it in a book), with an acknowledgment of its initial publication in this journal.
- Authors are permitted and encouraged to post their work online (e.g., in institutional repositories or on their website) prior to and during the submission process, as it can lead to productive exchanges, as well as earlier and greater citation of published work.