Analysis of sag mill machine performance using overall equipment effectiveness and failure model and effects analysis method
DOI:
https://doi.org/10.12928/ijio.v3i2.6701Keywords:
Efficiency Machine, SAG Mill, FMEA, OEEAbstract
The mining company uses a variety of grinding machines to process minerals, whereas the most common type of machine is the Semi-Autogenous Grinding SAG Mill machine. This machine is employed for the mining process of hard rock as raw material into gold, copper, and silver. However, the SAG Mill machines are often broken, even suddenly not working, with an average loss time of 97.30 hours which impacts a decrease in efficiency and production quality of up to 40%. It can cause losses that do not reach the production target. This research aims to measure the effectiveness of the SAG Mill machine and determine the failure using the OEE and FMEA methods. The results showed that the SAG Mill machine is still under standardized based on the Japan Institute of Plant Maintenance (JIPM), which is 85%. The FMEA method and RPN value apply to analyze downtime losses, and idling is the loss that highly affects the effectiveness of SAG Mill machines. Recommendations for the company are to increase the number of equipment that aims to prolong the machine's age and accelerate production. This research contributes to another solution to help maintenance managers by measuring the effectiveness and determining the failure of the SAG Mill machine
References
K. Krachangchan and N. Thawesaengskulthai, "Loss time reduction for improve overall equipment effectiveness (OEE)," 2018 5th International Conference on Industrial Engineering and Applications (ICIEA), 2018.
E. Westphal and H. Seitz, "A machine learning method for defect detection and visualization in selective laser sintering based on Convolutional Neural Networks," Additive Manufacturing, vol. 41, p. 101965, 2021.
O. Abdulhameed, A. Al-Ahmari, W. Ameen, and S. H. Mian, "Additive manufacturing: Challenges, trends, and applications," Advances in Mechanical Engineering, vol. 11, no. 2, p. 168781401882288, 2019.
P. H. Tsarouhas, "Overall Equipment Effectiveness (OEE) evaluation for an automated ice cream production line," International Journal of Productivity and Performance Management, vol. 69, no. 5, pp. 1009–1032, 2019.
D. I. Sukma, I. M. Fahturizal, H. Kurnia, I. Setiawan, and H. A. Prabowo, "Implementation of total productive maintenance to improve overall equipment effectiveness of linear accelerator synergy platform cancer therapy," International Journal of Engineering, vol. 35, no. 7, pp. 1246–1256, 2022.
P. W. Cleary and P. Owen, "Effect of particle shape on structure of the charge and nature of energy utilisation in a SAG Mill," Minerals Engineering, vol. 132, pp. 48–68, 2019.
C. Xie, Y. Zhao, T. Song, and Y. Zhao, "Investigation of the effect of filling level on the wear and vibration of a SAG Mill by Dem," Particuology, vol. 63, pp. 24–34, 2022.
Z. Tian Xiang and C. Jeng Feng, "Implementing total productive maintenance in a manufacturing small or medium-sized enterprise," Journal of Industrial Engineering and Management, vol. 14, no. 2, p. 152, 2021.
E. Kosicka, A. Gola, and J. Pawlak, "Application-based support of Machine Maintenance," IFAC-PapersOnLine, vol. 52, no. 10, pp. 131–135, 2019.
F. Pohlmeyer, R. Kins, F. Cloppenburg, and T. Gries, "Interpretable failure risk assessment for Continuous Production Processes based on Association Rule Mining," Advances in Industrial and Manufacturing Engineering, vol. 5, p. 100095, 2022.
V. Pascal, A. Toufik, A. Manuel, D. Florent, and K. Frédéric, "Improvement indicators for total productive maintenance policy," Control Engineering Practice, vol. 82, pp. 86–96, 2019.
A. Ali, "Application of total productive maintenance in service organization," Journal of Research in Industrial Engineering, vol. 8, no. 2, pp. 176–186, Jun. 2019.
S. Sakti, A. E. Panjaitan, A. M. Asih, and B. M. Sopha, "A computerized measurement system of machine performance for a textile industry," IOP Conference Series: Materials Science and Engineering, vol. 673, no. 1, p. 012078, 2019.
C. Jaqin , H. Hardi Purba, and A. Rozak , "Case study in increasing overall equipment effectiveness on progressive press machine using plan-do-check-act cycle," International Journal of Engineering, vol. 33, no. 11, pp. 2245–2251, Nov. 2020.
Z. Wang, Y. Ran, H. Yu, C. Jin, and G. Zhang, "Failure mode and effects analysis using function–motion–action decomposition method and integrated risk priority number for mechatronic products," Quality and Reliability Engineering International, vol. 37, no. 6, pp. 2875–2899, 2021.
L. Ciani, G. Guidi, and G. Patrizi, "A critical comparison of alternative risk priority numbers in failure modes, effects, and criticality analysis," IEEE Access, vol. 7, pp. 92398–92409, 2019.
A. J. Sang, K. M. Tay, C. P. Lim, and S. Nahavandi, "Application of a genetic-fuzzy FMEA to rainfed lowland rice production in Sarawak: Environmental, health, and Safety Perspectives," IEEE Access, vol. 6, pp. 74628–74647, 2018.
I. S. Muthalib, M. Rusman, and G. L. Griseldis, "Overall Equipment Effectiveness (OEE) analysis and failure mode and effect analysis (FMEA) on Packer machines for minimizing the six big losses - a cement industry case," IOP Conference Series: Materials Science and Engineering, vol. 885, no. 1, p. 012061, 2020.
S. Basak, M. Baumers, M. Holweg, R. Hague, and C. Tuck, "Reducing production losses in additive manufacturing using overall equipment effectiveness," Additive Manufacturing, vol. 56, p. 102904, 2022.
A. Wahid, “Penerapan total productive maintenance (TPM) Produksi Dengan Metode overall equipment effectiveness (OEE) Pada proses produksi botol (pt. XY pandaan – pasuruan),” Jurnal Teknologi Dan Manajemen Industri, vol. 6, no. 1, pp. 12–16, 2020.
L. V. Ginste, E.-H. Aghezzaf, and J. Cottyn, "The role of equipment flexibility in overall equipment effectiveness (OEE)-driven process improvement," Procedia CIRP, vol. 107, pp. 289–294, 2022.
B. F. Marfinov and A. J. Pratama, "Overall Equipment Effectiveness (OEE) analysis to minimize six big losses in continuous blanking machine," IJIEM - Indonesian Journal of Industrial Engineering and Management, vol. 1, no. 1, p. 25, 2020.
A. Wicaksono and F. Yuamita, "Pengendalian Kualitas Produksi Sarden Mengunakan metode failure mode and effect analysis (FMEA) Untuk Meminimumkan Cacat Kaleng di Pt. Maya Food Industries,” Jurnal Teknologi dan Manajemen Industri Terapan, vol. 1, no. I, pp. 1–6, 2022.
W. W. A. de Andrade, M. A. de Oliveira, and R. K. Vieira, "Evaluation of maintenance management of a thermoplastic industry using maintenance maturity model," Procedia Computer Science, vol. 204, pp. 635–642, 2022.
R. Fadli, J. Jufrizel, and W. P. Hastuti, “Analisa Sistem Instrumentasi Dan Keandalan boiler dengan metode fault tree analysis (FTA) Dan Metode Failure Mode and effect analysis (FMEA),” El Sains : Jurnal Elektro, vol. 2, no. 2, 2021.
M. E. Beatrix, H. Kartika, and Sunardiyanta, "Analysis of effectiveness measurement of stretch blow machine using overall equipment effectiveness (OEE) method," International Journal of Advances in Scientific Research and Engineering, vol. 06, no. 08, pp. 131–137, 2020.
F. Pohlmeyer, R. Kins, F. Cloppenburg, and T. Gries, "Interpretable failure risk assessment for Continuous Production Processes based on Association Rule Mining," Advances in Industrial and Manufacturing Engineering, vol. 5, p. 100095, 2022.
M. J. Ershadi, R. Aiasi, and S. Kazemi, “Root cause analysis in quality problem solving of research information systems: A case study,” International Journal of Productivity and Quality Management, vol. 24, no. 2, p. 284, 2018.
A. Suherman and B. J. Cahyana, “Pengendalian Kualitas Dengan Metode Failure Mode Effect And Analysis (FMEA) Dan Pendekatan Kaizen untuk Mengurangi Jumlah Kecacatan dan Penyebabnya,” Seminar Nasional Sains dan Teknologi , pp. 1–9, Oct. 2019.
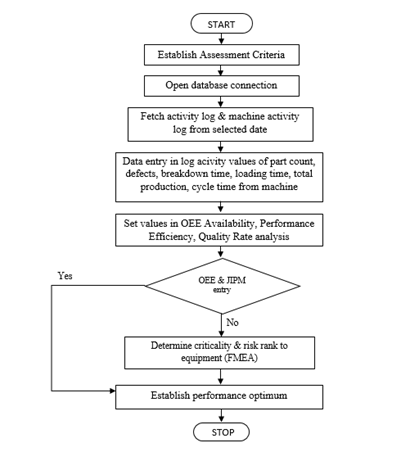
Downloads
Published
How to Cite
Issue
Section
License
Copyright (c) 2022 Sinta Luluk Fuadiya, Endang Pudji Widjajati

This work is licensed under a Creative Commons Attribution-ShareAlike 4.0 International License.
License and Copyright Agreement
In submitting the manuscript to the journal, the authors certify that:
- They are authorized by their co-authors to enter into these arrangements.
- The work described has not been formally published before, except in the form of an abstract or as part of a published lecture, review, thesis, or overlay journal. Please also carefully read the International Journal of Industrial Optimization (IJIO) Author Guidelines at http://journal2.uad.ac.id/index.php/ijio/about/submissions#onlineSubmissions
- That it is not under consideration for publication elsewhere,
- That its publication has been approved by all the author(s) and by the responsible authorities tacitly or explicitly of the institutes where the work has been carried out.
- They secure the right to reproduce any material that has already been published or copyrighted elsewhere.
- They agree to the following license and copyright agreement.
Copyright
Authors who publish with the International Journal of Industrial Optimization (IJIO) agree to the following terms:
- Authors retain copyright and grant the journal right of first publication with the work simultaneously licensed under a Creative Commons Attribution License (CC BY-SA 4.0) that allows others to share the work with an acknowledgment of the work's authorship and initial publication in this journal.
- Authors are able to enter into separate, additional contractual arrangements for the non-exclusive distribution of the journal's published version of the work (e.g., post it to an institutional repository or publish it in a book), with an acknowledgment of its initial publication in this journal.
- Authors are permitted and encouraged to post their work online (e.g., in institutional repositories or on their website) prior to and during the submission process, as it can lead to productive exchanges, as well as earlier and greater citation of published work.