Development of genetic algorithm for human-robot collaboration assembly line design
DOI:
https://doi.org/10.12928/ijio.v5i2.10027Keywords:
Assembly line balancing, Human-Robot Collaboration, Genetic Algorithm, Cycle TimeAbstract
An assembly line requires flexibility due to a shorter product life cycle. A way to increase flexibility is to utilize collaborative robots or cobots. Due to frequent product changes, redesigning an assembly line requires an efficient algorithm. This research aims to develop a genetic algorithm (GA) for solving a human-cobots assembly line design. The setup time of cobots is considered due to the flexibility of conducting multiple tasks by exchanging tools / end-effectors. The main contribution of the research is the efficient GA for solving assembly lines considering setup time. Secondly, the study proposed an upper limit parameter that enables faster computation without sacrificing the quality of the solution. The computational results showed that the algorithm could achieve an optimal solution with the number of tasks less than 35. Experiments of several data prove the proposed GA obtained solutions with an average gap of 3.83% to the optimal solution. Also, a faster computation time with an average difference of 64.66%. The proposed GA obtained a reasonable solution with fast computing time that helps improve efficiency and effectiveness in decision-making related to frequent redesigning of assembly lines.
References
F. Lestari, “Perancangan Lintas Perakitan pada Product Family berdasarkan Common Subassembly,” SNTIKI III, pp. 430–436, 2011, [Online]. Available: https://ejournal.uin-suska.ac.id/
M. Eghtesadifard, M. Khalifeh, and M. Khorram, “A systematic review of research themes and hot topics in assembly line balancing through the Web of Science within 1990-2017,” Computers & Industrial Engineering, 2019, doi: 10.1016/j.cie.2019.106182.
N. H. Kamarudin and M. F. F. A. Rashid, “Assembly line balancing with resource constraints using new rank-based crossovers,” Journal of Physics: Conference Series, vol. 908, 2017, doi: 10.1088/1742-6596/908/1/012059.
A. Ma’ruf, C. Nugraha, and A. S. Tarigan, “The Development of Human-Robot Collaborative Assembly Line Model by Considering Availability of Robots , Tools , and Setup Time,” Jurnal Ilmiah Teknik Industri, pp. 319–327, 2022, doi: 10.23917/jiti.v21i2.19619.
M. Kheirabadi, S. Keivanpour, Y. A. Chinniah, and J. M. Frayret, “Human-robot collaboration in assembly line balancing problems: Review and research gaps,” Computers & Industrial Engineering, vol. 186, Dec. 2023, doi: 10.1016/j.cie.2023.109737.
T. Kiyokawa et al., “Difficulty and complexity definitions for assembly task allocation and assignment in human–robot collaborations: A review,” Robotics and Computer-Integrated Manufacturing, vol. 84. Elsevier Ltd, Dec. 01, 2023. doi: 10.1016/j.rcim.2023.102598.
L. Gualtieri, E. Rauh, and R. Vidoni, “Methodology for the definition of the optimal assembly cycle and calculation of the optimized assembly cycle time in human-robot collaborative assembly,” International Journal of Advanced Manufacturing Technology, 2021, doi: 10.1007/s00170-021-06653-y.
A. Nourmohammadi, M. Fathi, and A. H. C. Ng, “Balancing and scheduling assembly lines with human-robot collaboration tasks,” Computers & Operations Research, vol. 140, Apr. 2022, doi: 10.1016/j.cor.2021.105674.
S. Puttero, E. Verna, G. Genta, and M. Galetto, “Towards the modelling of defect generation in human-robot collaborative assembly,” in Procedia CIRP, Elsevier B.V., 2023, pp. 247–252. doi: 10.1016/j.procir.2023.06.043.
M. D. Mura and G. Dini, “CIRP Annals - Manufacturing Technology Designing assembly lines with humans and collaborative robots : A genetic approach,” CIRP Annals - Manufacturing Technology, vol. 68, no. 1, pp. 1–4, 2019, doi: 10.1016/j.cirp.2019.04.006.
L. Gualtieri, F. Fraboni, M. De Marchi, and E. Rauch, “Development and evaluation of design guidelines for cognitive ergonomics in human-robot collaborative assembly systems,” Applied Ergonomics, vol. 104, Oct. 2022, doi: 10.1016/j.apergo.2022.103807.
A. Scholl, Balancing and Sequencing of Assembly Lines. Darmstadt: Physica-Verlag Heidelberg, 1999, doi: 10.1007/978-3-662-11223-6.
O. Bagaria, “Importance of Cycle time Reduction for Productivity Improvement,” JETIR, vol. 6, no. 4, pp. 802–805, 2019, [Online]. Available: https://www.jetir.org/papers/JETIREO06173.pdf
R. Chase, F. R. Jacobs, and N. Aquilano, Operations Management for Competitive Advantage, 11th ed. New York: The McGraw-Hill Companies, Inc., 2006.
C. Andres, C. Miralles, and R. Pastor, “Balancing and scheduling tasks in assembly lines with sequence-dependent setup times,” European Journal of Operational Research, vol. 187, pp. 1212–1223, 2008, doi: 10.1016/j.ejor.2006.07.044.
D. Andronas, S. Xythalis, P. Karagiannis, G. Michalos, and S. Makris, “Robot gripper with high speed, in-hand object manipulation capabilities,” in Procedia CIRP, Elsevier B.V., 2020, pp. 482–486. doi: 10.1016/j.procir.2020.08.007.
Z. Y. Deng, L. W. Kang, H. H. Chiang, and H. C. Li, “Integration of Robotic Vision and Automatic Tool Changer Based on Sequential Motion Primitive for Performing Assembly Tasks,” in IFAC-PapersOnLine, Elsevier B.V., Jul. 2023, pp. 5320–5325. doi: 10.1016/j.ifacol.2023.10.175.
B. Zhang, Y. Xie, J. Zhou, K. Wang, and Z. Zhang, “State-of-the-art robotic grippers, grasping and control strategies, as well as their applications in agricultural robots: A review,” Computers and Electronics in Agriculture, vol. 177. Elsevier B.V., Oct. 01, 2020. doi: 10.1016/j.compag.2020.105694.
R. C. Nugraha, A. Ma’ruf, A. C. Nugraha, and A. H. Halim, “A mixed-integer linear programming formulation for assembly line balancing problem with human- robot shared tasks,” Journal of Physics: Conference Series, 2020, doi: 10.1088/1742-6596/1858/1/012021.
A. Yaphiar, Susanto; Nugraha, Cahyadi; Ma’ruf, “Mixed Model Assembly Line Balancing for Human-Robot Shared Tasks,” iMEC-APCOMS, pp. 245–252, 2019, doi: 10.1007/978-981-15-0950-6_38.
C. Weckenborg, K. Kieckha¨fer, C. Muller, M. Grunewald, and T. S. Splenger, “Balancing of assembly lines with collaborative robots,” Business Research, pp. 93–132, 2020, doi: 10.1007/s40685-019-0101-y.
I. Dimény, T. Koltai, C. Sepe, T. Murino, V. Gallina, and T. Komenda, “MILP model to decrease the MILP model to decrease the number of workers MILP model to decrease the number of workers in in assembly assembly lines lines with collaboration of workers in assembly lines with human-robot MILP model to decrease the number col,” in IFAC PapersOnLine, Elsevier Ltd, 2021, pp. 169–174. doi: 10.1016/j.ifacol.2021.08.019.
Z. Li, M. N. Janardhanan, Q. Tang, and S. G. Ponnambalam, “Model and metaheuristics for robotic two-sided assembly line balancing problems with setup times,” Swarm and Evolutionary Computation, vol. 50, no. October 2018, 2019, doi: 10.1016/j.swevo.2019.100567.
M. N. Janardhanan, Z. Li, G. Bocewicz, Z. Banaszak, and P. Nielsen, “Metaheuristic algorithms for balancing robotic assembly lines with sequence-dependent robot setup times,” Applied Mathematical Modelling, vol. 65, pp. 256–270, 2019, doi: 10.1016/j.apm.2018.08.016.
C. Zhang, J. Dou, and P. Wang, “Configuration design of reconfigurable single-product robotic assembly line for capacity scalability,” Computers & Industrial Engineering, vol. 185, Nov. 2023, doi: 10.1016/j.cie.2023.109682.
N. P. Basán, M. E. Cóccola, A. García del Valle, and C. A. Méndez, “Scheduling of flexible manufacturing plants with redesign options: A MILP-based decomposition algorithm and case studies,” Computers & Chemical Engineering, vol. 136, May 2020, doi: 10.1016/j.compchemeng.2020.106777.
S. E. Hashemi-Petroodi, S. Thevenin, and A. Dolgui, “Mixed-Model Assembly Line Design with New Product Variants in Production Generations,” in IFAC-PapersOnLine, Elsevier B.V., 2022, pp. 25–30. doi: 10.1016/j.ifacol.2022.09.363.
Z. Mao, Y. Sun, K. Fang, D. Huang, and J. Zhang, “Model and metaheuristic for human–robot collaboration assembly line worker assignment and balancing problem,” Computers & Operations Research, vol. 165, p. 106605, May 2024, doi: 10.1016/j.cor.2024.106605.
L. Rozo et al., “The e-Bike motor assembly: Towards advanced robotic manipulation for flexible manufacturing,” Robotics and Computer-Integrated Manufacturing, vol. 85, Feb. 2024, doi: 10.1016/j.rcim.2023.102637.
A. Nourmohammadi, M. Fathi, A. H. C. Ng, and E. Mahmoodi, “A genetic algorithm for heterogenous human-robot collaboration assembly line balancing problems,” in Procedia CIRP, Elsevier B.V., 2022, pp. 1444–1448. doi: 10.1016/j.procir.2022.05.172.
S.-G. Liao, Y.-B. Zhang, C.-Y. Sang, and H. Liu, “A Genetic Algorithm for Balancing and Sequencing of Mixed-Model Two-Sided Assembly Line with Unpaced Synchronous Transfer,” Applied Soft Computing, vol. 146, 2023, doi: 10.1016/j.asoc.2023.110638.
S. S. Tjandra, F. Setiawan, and H. Salsabila, “Jurnal Optimasi Sistem Industri Application of Genetic Algorithms to Solve MTSP Problems with Priority ( Case Study at the Jakarta Street Lighting Service ),” Jurnal Optimasi Sistem Industri, vol. 21, pp. 75–86, 2022, doi: 10.25077/josi.v21.n2.p75-86.2022.
N. Harale, S. Thomassey, and X. Zeng, “Dynamic small-series fashion order allocation and supplier selection : a ga-topsis-based model,” International Journal of Industrial Optimization, vol. 4, no. 2, pp. 82–102, 2023, doi: 10.12928/ijio.v4i2.7640.
P. Segura, O. Lobato-calleros, A. Ramírez-serrano, and I. Soria, “Human-robot collaborative systems : Structural components for current manufacturing applications,” Advances in Industrial and Manufacturing Engineering, vol. 3, 2021, doi: 10.1016/j.aime.2021.100060.
N. Berx, W. Decre, and L. Pintelon, “Examining the Role of Safety in the Low Adoption Rate of Collaborative Robots,” in Procedia CIRP, Elsevier B.V., 2022, pp. 51–57. doi: 10.1016/j.procir.2022.02.154.
K. Merckaert, B. Convens, M. M. Nicotra, and B. Vanderborght, “Real-time constraint-based planning and control of robotic manipulators for safe human–robot collaboration,” Robotics and Computer-Integrated Manufacturing, vol. 87, Jun. 2024, doi: 10.1016/j.rcim.2023.102711.
K. Katsampiris-Salgado et al., “Collision detection for collaborative assembly operations on high-payload robots,” Robotics and Computer-Integrated Manufacturing, vol. 87, Jun. 2024, doi: 10.1016/j.rcim.2023.102708.
J. Shu, W. Li, and Y. Gao, “Collision-free trajectory planning for robotic assembly of lightweight structures,” Automation in Construction, vol. 142, Oct. 2022, doi: 10.1016/j.autcon.2022.104520.
N. Boysen, P. Schulze, and A. Scholl, “Assembly line balancing : What happened in the last fifteen years?,” European Journal of Operational Research, vol. 301, pp. 797–814, 2022, doi: 10.1016/j.ejor.2021.11.043.
D. M. Utama, L. R. Ardiansyah, and A. K. Garside, “Penjadwalan Flow shop Untuk Meminimasi Total Tardiness Menggunakan Algoritma Cross Entropy – Algoritma Genetika,” Jurnal Optimasi Sistem Industri, vol. 2, pp. 133–141, 2019, doi: 10.25077/josi.v18.n2.p133-141.2019.
J. C. Chen, Y. Chen, T. Chen, and Y. Kuo, “Applying two-phase adaptive genetic algorithm to solve multi-model assembly line balancing problems in TFT – LCD module process,” Journal of Manufacturing Systems, vol. 52, no. May, pp. 86–99, 2019, doi: 10.1016/j.jmsy.2019.05.009.
D. Shukla, A.; Pandey, H. M.; Mehrotra, “Comparative Review of Selection Comparative Review of Selection,” 2015 1st International Conference on Futuristic trend in Computational Analysis and Knowledge Management. 2015. doi: 10.1109/ABLAZE.2015.7154916.
D. Chakraborti, P. Biswas, and B. B. Pal, “FGP Approach for Solving Fractional Multiobjective Decision Making Problems using GA with Tournament Selection and Arithmetic Crossover,” Procedia Technology, vol. 10, pp. 505–514, 2013, doi: 10.1016/j.protcy.2013.12.389.
A. K. Pachuau, Joseph L.; Roy, Arnab; Saha, “An Overview of Crossover Techniques in Genetic Algorithm,” Proceedings of CoMSO: Modeling, Simulation Modeling, Simulation. pp. 581–598, 2020. doi: 10.1007/978-981-15-9829-6_46.
S. M. Anwar, A. M. Ali, and M. A. Awad, “Single Model Assembly Line Balancing Using Enhanced Genetic Algorithm,” Saudi Journal of Engineering and Technology, no. December 2019, pp. 494–501, 2020, doi: 10.36348/sjet.2019.v04i12.003.
S. L. Yadav and A. Sohal, “Comparative Study of Different Selection Techniques in Genetic Algorithm,” International Journal of Engineering Science and Mathematics, vol. 6, no. 3, pp. 174–180, 2017, [Online]. Available: https://ijesm.co.in/uploads/68/3180_pdf.pdf
Y. Su, Ping; Lu, “Combining Genetic Algorithm and Simulation for the Mixed-model Assembly Line Balancing Problem,” Third International Conference on Natural Computation, no. Icnc, pp. 174–180, 2007, doi: 10.1109/ICNC.2007.306.
Y. J. Kim, Y. K.; Lee, S. Y.; Kim, “A Genetic Algorithm for Improving the Workload Smoothness in Mixed Model Assembly Lines.,” Journal of the Korean Institute of Industrial Engineers, pp. 515–532, 1997. Available: https://koreascience.kr/article/JAKO199729464079022.page
B. Durakovic, “Design of Experiments Application , Concepts , Examples : State of the Art,” Periodicals of Engineering and Natural Sciences, vol. 5, pp. 421–439, 2021, doi: 10.21533/pen.v5i3.145.
Y. Zhang and R. Chen, “Energy-efficient scheduling of imprecise mixed-criticality real-time tasks based on genetic algorithm,” Journal of Systems Architecture, vol. 143, 2023, doi: 10.1016/j.sysarc.2023.102980.
C. Seeber, M. Albus, M. Fechter, A. Neb, and S. I. Yoshida, “Automated 2D Layout Design of Assembly Line Workstations through Physical Principles,” in Procedia CIRP, Elsevier B.V., 2021, pp. 1197–1202. doi: 10.1016/j.procir.2021.11.201.
B. Su, S. H. Jung, L. Lu, H. Wang, L. Qing, and X. Xu, “Exploring the impact of human-robot interaction on workers’ mental stress in collaborative assembly tasks,” Applied Ergonomics, vol. 116, Apr. 2024, doi: 10.1016/j.apergo.2024.104224.
H. Duan, Y. Yang, D. Li, and P. Wang, “Human-robot object handover: Recent progress and future direction,” Biomimetic Intelligence and Robotics, p. 100145, Feb. 2024, doi: 10.1016/j.birob.2024.100145.
V. Gopinath, K. Johansen, M. Derelöv, Å. Gustafsson, and S. Axelsson, “Safe Collaborative Assembly on a Continuously Moving Line with Large Industrial Robots,” Robotics and Computer-Integrated Manufacturing, vol. 67, Feb. 2021, doi: 10.1016/j.rcim.2020.102048.
M. Eswaran et al., “Optimal layout planning for human robot collaborative assembly systems and visualization through immersive technologies,” Expert Systems with Applications, vol. 241, May 2024, doi: 10.1016/j.eswa.2023.122465.
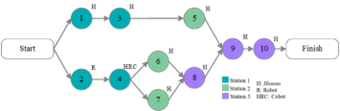
Downloads
Published
How to Cite
Issue
Section
License
Copyright (c) 2024 Anas Ma'ruf, Diniarie Budhiarti

This work is licensed under a Creative Commons Attribution-ShareAlike 4.0 International License.
License and Copyright Agreement
In submitting the manuscript to the journal, the authors certify that:
- They are authorized by their co-authors to enter into these arrangements.
- The work described has not been formally published before, except in the form of an abstract or as part of a published lecture, review, thesis, or overlay journal. Please also carefully read the International Journal of Industrial Optimization (IJIO) Author Guidelines at http://journal2.uad.ac.id/index.php/ijio/about/submissions#onlineSubmissions
- That it is not under consideration for publication elsewhere,
- That its publication has been approved by all the author(s) and by the responsible authorities tacitly or explicitly of the institutes where the work has been carried out.
- They secure the right to reproduce any material that has already been published or copyrighted elsewhere.
- They agree to the following license and copyright agreement.
Copyright
Authors who publish with the International Journal of Industrial Optimization (IJIO) agree to the following terms:
- Authors retain copyright and grant the journal right of first publication with the work simultaneously licensed under a Creative Commons Attribution License (CC BY-SA 4.0) that allows others to share the work with an acknowledgment of the work's authorship and initial publication in this journal.
- Authors are able to enter into separate, additional contractual arrangements for the non-exclusive distribution of the journal's published version of the work (e.g., post it to an institutional repository or publish it in a book), with an acknowledgment of its initial publication in this journal.
- Authors are permitted and encouraged to post their work online (e.g., in institutional repositories or on their website) prior to and during the submission process, as it can lead to productive exchanges, as well as earlier and greater citation of published work.