Implementation of 5s and kaızen methods for developing a novel wage assessment method in a steel construction factory: an application in Turkey
DOI:
https://doi.org/10.12928/ijio.v5i2.10023Keywords:
Job Evaluation and Analysis, Wage Assessment, 5S Method, Kaizen, Steel ConstructionAbstract
The study aims to implement the 5S (seiri, seiton, seiso, seiketsu, and shitsuke) method and KAIZEN for emphasizing the troubles and defective products, establishing work standards, implementing fair wage assessments based on job analysis and job evaluations in a steel construction factory. A more objective wage assessment method is developed, and workers' unrest can be resolved fairly. 5S and KAIZEN studies have been applied for two years in a steel construction factory. Then, the evaluation of success factors within the internal structure of wage brackets utilized last year's 5S scores to enhance employees' confidence in the objectiveness of the wage system assessment. A reformer method for assessing wages has been created and implemented, integrating lean manufacturing principles and a job analysis and evaluation system. The framework has been tested and implemented only for a steel construction factory. In the future, studies could be conducted to assess different sector factories. The proposed framework has been successfully implemented in a medium-large scale manufacturing factory. A novel wage assessment framework that involves lean application studies integrated into the job evaluation method has been proposed in a medium-sized manufacturing factory.
References
M. A. Hitt, R. D. Ireland, and R. E. Hoskisson, Strategic Management Cases: Competitiveness and Globalization, 10th ed. Mason, Ohio: Cengage Learning, 2013.
E. Korkmaz, “Occupatıonal Health And Safety Assesment Based On 5s Systematıc In The Natural Gas Meter Productıon Facılıty,” İstanbul Technical University, 2016.
J. Michalska and D. Szewieczek, “The 5S methodology as a tool for improving the organisation,” Journal of Achivements in Materials and Manufacturing Engineering, vol. 24, no. 2, pp. 211–214, 2007, Accessed: Dec. 18, 2018. [Online]. Available: http://citeseerx.ist.psu.edu/
D. A. DeCenzo, S. P. Robbins, and S. L. Verhulst, Fundamentals of Human Resource Management, 12th ed. John Wiley & Sons, 2016.
P. Gaiardelli, B. Resta, and S. Dotti, “Exploring the role of human factors in lean management,” International Journal of Lean Six Sigma, vol. 10, no. 1, pp. 339–366, 2019, doi: 10.1108/IJLSS-08-2017-0094.
C. A. Moya, D. Galvez, L. Muller, and M. Camargo, “A new framework to support Lean Six Sigma deployment in SMEs,” International Journal of Lean Six Sigma, vol. 10, no. 1, pp. 58–80, 2019, doi: 10.1108/IJLSS-01-2018-0001.
J. K. Liker, The Toyota Way. Newyork: Mc Graw Hill, 2004. doi: 10.1036/0071392319.
E. G. Satolo, L. E. de S. Hiraga, G. A. Goes, and W. L. Lourenzani, “Lean production in agribusiness organizations: multiple case studies in a developing country,” International Journal of Lean Six Sigma, vol. 8, no. 3, pp. 335–358, 2017, doi: 10.1108/IJLSS-03-2016-0012.
M. S. Obeidat, R. Al-Aomar, and Z. J. Pei, “Lean Manufacturing Implementation in the Sewing Industry,” Journal of Enterprise Transformation, vol. 4, no. 2, pp. 151–171, 2014, doi: 10.1080/19488289.2014.890980.
A. P. Chaple, B. E. Narkhede, and M. M. Akarte, “Status of implementation of Lean manufacturing principles in the context of Indian industry: A Literature Review,” in IIT Guwahati, Assam: 5 th International & 26th All India Manufacturing Technology, Design and Research Conference, 2014, p. 6. Accessed: Feb. 18, 2019. [Online]. Available: www.search.proquest.com
P. Chikhalikar and S. Sharma, “Implementation of Lean Manufacturıng in an Engine Manufacturing Unit-A Review,” Int. J. Mech. Eng. & Rob. Res, vol. 4, no. 1, pp. 404–419, 2015, Accessed: Dec. 20, 2018. [Online]. Available: www.ijmerr.com
R. Kumar and V. Kumar, “Lean manufacturing in Indian context: A survey,” Management Science Letters, vol. 5, no. 4, pp. 321–330, 2015, doi: 10.5267/j.msl.2015.2.009.
M. Faishal, E. Mohamad, H. M. Asih, A. A. A. Rahman, A. Z. Ibrahim, and O. Adiyanto, “The use of Lean Six Sigma to improve the quality of coconut shell briquette products,” Multidisciplinary Science Journal, vol. 6, no. 2, 2024, doi: 10.31893/multıscıence.2024005.
A. Karim and K. Arif‐Uz‐Zaman, “A methodology for effective implementation of lean strategies and its performance evaluation in manufacturing organizations,” Business Process Management Journal, vol. 19, no. 1, pp. 169–196, 2013, doi: 10.1108/14637151311294912.
R. Salem, F. Musharavati, A. M. Hamouda, and K. N. Al-Khalifa, “An empirical study on lean awareness and potential for lean implementations in Qatar industries,” The International Journal of Advanced Manufacturing Technology, vol. 82, no. 9, pp. 1607–1625, 2016, doi: 10.1007/s00170-015-7421-7.
N. Verma and V. Sharma, “Sustainable competitive advantage by implementing lean manufacturing ‘A Case study for Indian SME,’” Mater Today Proc, vol. 4, no. 8, pp. 9210–9217, 2017, doi: 10.1016/j.matpr.2017.07.279.
P. Ahlström, “Sequences in the implementation of Lean Production,” European Management Journal, vol. 16, no. 3, pp. 327–334, 1998, doi: 0263-2373/9800009-7.
R. Shah and P. T. Ward, “Lean manufacturing: context, practice bundles, and performance,” Journal of Operations Management, vol. 21, no. 2, pp. 129–149, Mar. 2003, doi: 10.1016/S0272-6963(02)00108-0.
R. Shah and P. T. Ward, “Defining and developing measures of lean production,” Journal of Operations Management, vol. 25, no. 4, pp. 785–805, 2007, doi: 10.1016/j.jom.2007.01.019.
R. Gapp, R. Fisher, and K. Kobayashi, “Implementing 5S within a Japanese context: an integrated management system,” Journal of Manufacturing Technology Management, vol. 27, no. 3, pp. 364–378, 2017, doi: 10.1108/00251740810865067.
S. Benligiray, Ücret Yönetimi, 1st ed. İstanbul: Beta Basım Yayım Dağıtım A.Ş., 2007.
E. Lanham, Job Evaluation. Newyork: McGraw Hill Book Company Inc., 1955.
S. Çolakoğlu, “Bir işletmede iş değerleme sistemi tasarımı, uygulanması ve doğrusal programlama ile ücret sistematiğinin oluşturulması,” Master Thesıs, Çukurova University, 2006.
P. Dennis, Lean Production Simplified, 2nd ed. New York: Productivity Press, 2007.
S. Gupta and S. K. Jain, “An application of 5S concept to organize the workplace at a scientific instruments manufacturing company,” International Journal of Lean Six Sigma, vol. 6, no. 1, pp. 73–88, Jan. 2015, doi: 10.1108/IJLSS-08-2013-0047.
H. Hirano, JIT Implementation Manual – The complete guide to just-in-time manufacturing, 2nd ed. New York: Productivity Press, 2009. doi: 10.1201/b10229
Z. Zhang, X. Liu, and S. Yang, “A Note on the 1-9 scale and index scale in AHP,” in Conferance on Multiple Criteria Decision Making, Berlin: Springer, 2009, pp. 630–634. doi: 10.1007/978-3-642-02298-2_92.
A. J. Arthurs, Job Design and Evaluation : Organizational Aspects, Second Edi., vol. 12. Elsevier, 2015. doi: 10.1016/B978-0-08-097086-8.73077-7.
M. Beer, B. Spector, P. R. Lawrence, D. Q. Mills, and R. E. Walton, Human Resource Management: A General Manager’s Perspective : Text and Cases. London: Collier Macmillan, 1985.
E. L. I. Lawler, “From job-based to competency-based organizations,” Journal of Organizational Behaviour, vol. 15, no. 1, pp. 3–15, Jan. 1994, doi: 10.1002/job.4030150103
E. E. Lawler, “What’s Wrong with Point-Factor Job Evaluation,” Compens Benefits Rev, vol. 18, no. 5, pp. 20–28, Oct. 1986, doi: 10.1177/088636878601800502.
M. Sholihin and R. Pike, “Fairness in performance evaluation and its behavioural consequences,” Accounting and Business Research, vol. 39, no. 4, pp. 397–413, 2009, doi: 10.1080/00014788.2009.9663374.
S. Çolakoğlu, “Bir işletmede iş değerleme sistemi tasarımı, uygulanması ve doğrusal programlama ile ücret sistematiğinin oluşturulması,” Çukurova University, 2006.
B. K. Suthar, T. L. Chakravarthi, and S. Pradhan, “Impacts of job analysis on organizational performance : An inquiry on indian public sector enterprises,” Procedia Economics and Finance, vol. 11, no. 14, pp. 166–181, 2014, doi: 10.1016/S2212-5671(14)00186-5.
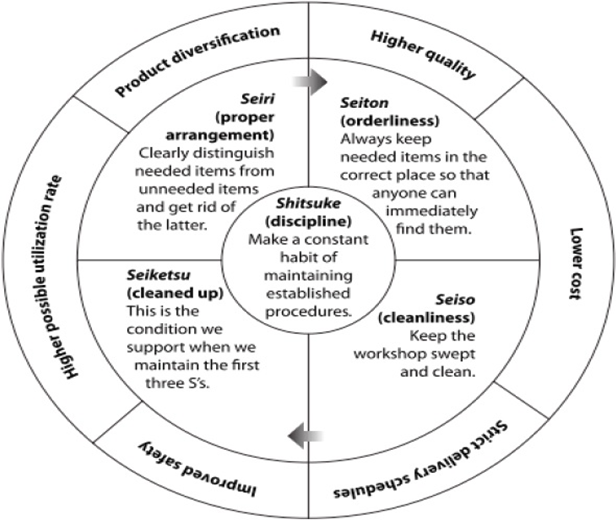
Downloads
Published
How to Cite
Issue
Section
License
Copyright (c) 2024 Mehmet Burçin Önay, Serap Ulusam Seçkiner

This work is licensed under a Creative Commons Attribution-ShareAlike 4.0 International License.
License and Copyright Agreement
In submitting the manuscript to the journal, the authors certify that:
- They are authorized by their co-authors to enter into these arrangements.
- The work described has not been formally published before, except in the form of an abstract or as part of a published lecture, review, thesis, or overlay journal. Please also carefully read the International Journal of Industrial Optimization (IJIO) Author Guidelines at http://journal2.uad.ac.id/index.php/ijio/about/submissions#onlineSubmissions
- That it is not under consideration for publication elsewhere,
- That its publication has been approved by all the author(s) and by the responsible authorities tacitly or explicitly of the institutes where the work has been carried out.
- They secure the right to reproduce any material that has already been published or copyrighted elsewhere.
- They agree to the following license and copyright agreement.
Copyright
Authors who publish with the International Journal of Industrial Optimization (IJIO) agree to the following terms:
- Authors retain copyright and grant the journal right of first publication with the work simultaneously licensed under a Creative Commons Attribution License (CC BY-SA 4.0) that allows others to share the work with an acknowledgment of the work's authorship and initial publication in this journal.
- Authors are able to enter into separate, additional contractual arrangements for the non-exclusive distribution of the journal's published version of the work (e.g., post it to an institutional repository or publish it in a book), with an acknowledgment of its initial publication in this journal.
- Authors are permitted and encouraged to post their work online (e.g., in institutional repositories or on their website) prior to and during the submission process, as it can lead to productive exchanges, as well as earlier and greater citation of published work.