Implementation of Digital Feedback Control with Change Rate Limiter in Regulating Water Flow Rate Using Arduino
DOI:
https://doi.org/10.12928/biste.v6i1.10234Keywords:
Error Feedback, Water Flow Rate, Change Rate Limiter, Mean Absolute Error (MAE), Root Mean Square Error (RMSE)Abstract
Water flow rate control is crucial in applications where it determines operational efficiency in applications such as agriculture, hydroponics, industrial processes, and hydrology. This research presents two algorithms for a simple and reliable digital water flow control: Error-Sign-based Control (ESC) and Error-Value-based Control (EVC). These algorithms are equipped with a change rate limiter to avoid excessive control output increase. They were compared qualitatively with the conventional digital PID controller. Subsequently, they were implemented and tested in a water circulation system. The control loop consisted of a microcontroller, water flow rate sensor, and submersible DC water pump with a supporting motor driver. The controllers were given a control task to follow a 150-second reference trajectory with a changing set point every 30 seconds. The performance measures of Mean Absolute Error (MAE) and Root Mean Square Error (RMSE) were utilized to assess the performance of the control algorithms. EVC with a change rate limiter of 10% delivered the best performance with an MAE of 0.40 and RMSE of 0.97. EVC provides simple and reliable control of the water flow rate system due to its easy tuning, quick tracking response to set point changes, and solid regulating performance. Further work in the implementation of the control scheme in other applications is encouraged.
References
C. W. Lumoindong and E. Sitompul, “A prototype of an IOT-based pet robot with customizable functions (CoFiBot V2),” International Journal of Mechanical Engineering and Robotics Research, pp. 510–518, 2021, https://doi.org/10.18178/ijmerr.10.9.510-518.
J. Kassila, N. Khallaf, K. Knibass, F. E. Aamri, and Y. Ouagajjou, “Effect of water flow rate on nursing spat mussels, mytilus galloprovincialis,” Thalassas: An International Journal of Marine Sciences, vol. 39, no. 2, pp. 1237–1243, 2023, https://doi.org/10.1007/s41208-023-00559-0.
Z. Jianhui and C. Xin, “Monitoring and control of gas flow rate in a pyrocarbon coating furnace for heart valves,” in Proc. of International Conference on Consumer Electronics, Communications and Networks (CECNet), 2011, https://doi.org/10.1109/CECNET.2011.5768609.
J. Ma and Y. Chen, “Influence of verification volume and flow rate on verification facility for water meters of piston,” in Proc. of the 19th International Flow Measurement Conference 2022 on Flow Measurement - FLOMEKO 2022, 2023, https://doi.org/10.21014/tc9-2022.074.
Y. Sueki and Y. Noda, “Development of flow rate feedback control in tilting-ladle-type pouring robot with direct manipulation of pouring flow rate,” in Proc. of the 16th International Conference on Informatics in Control, Automation and Robotics, 2019, https://doi.org/10.5220/0007951004600467.
E. A. Feukeu, L. L. Snyman, and H. Twinomurinzi, “Overcoming water scarcity with dynamic water flow rate control (DWFRC),” International Journal of Social Ecology and Sustainable Development, vol. 13, no. 1, pp. 1–16, 2022, https://doi.org/10.4018/IJSESD.289642.
D.-K. Kim and D.-H. Kang, “Investigation of a new UVC leds array continuous type water disinfection system for inactivating escherichia coli O157:H7 according to flow rate and electrical energy efficiency analysis,” Food Control, vol. 119, p. 107470, 2021, https://doi.org/10.1016/j.foodcont.2020.107470.
M. Galina, C. Safitri, I. Bukhori, A. Silitonga, and A. Suhartomo, “An an implementation of smart agriculture for optimizing growth using Sonic Bloom and IoT integrated,” Jurnal Infotel, vol. 14, no. 1, pp. 65–74, 2022, https://doi.org/10.20895/infotel.v14i1.725.
G. Swaminathan and G. Saurav, “Development of sustainable hydroponics technique for urban agrobusiness,” Evergreen, vol. 9, no. 3, pp. 629–635, 2022, https://doi.org/10.5109/4842519.
Vagisha, E. Rajesh, S. Basheer, and K. Baskar, “Hydroponics soilless smart farming in improving productivity of crop using Intelligent Smart Systems,” in Proc. of 3rd International Conference on Innovative Practices in Technology and Management (ICIPTM), 2023, https://doi.org/10.1109/ICIPTM57143.2023.10117747.
J. Li, Z. Mao, Z. Cao, K. Tei, and S. Honiden, “Self-adaptive hydroponics care system for human-hydroponics coexistence,” in Proc. of IEEE 3rd Global Conference on Life Sciences and Technologies (LifeTech), 2021, https://doi.org/10.1109/LifeTech52111.2021.9391909.
G. Niu and J. Masabni, “Hydroponics,” Plant Factory Basics, Applications and Advances, pp. 153–166, 2022, https://doi.org/10.1016/B978-0-323-85152-7.00023-9.
I. Aksikas, “Error-feedback temperature regulation for a reverse flow reactor driven by a distributed parameter exosystem,” Journal of Process Control, vol. 117, pp. 132–139, 2022, https://doi.org/10.1016/j.jprocont.2022.07.010.
A. Alotaibi, A. Alkandri, and M. Alsubaie, “Load disturbance conditions for current error feedback and past error feedforward state-Feedback Iterative Learning Control,” Intelligent Control and Automation, vol. 12, no. 02, pp. 65–72, 2021, https://doi.org/10.4236/ica.2021.122004.
J. Moreno-Valenzuela, R. Pérez-Alcocer, M. Guerrero-Medina and A. Dzul, “Nonlinear PID-Type Controller for Quadrotor Trajectory Tracking, “ IEEE/ASME Transactions on Mechatronics, vol. 23, no. 5, pp. 2436-2447, 2018, https://doi.org/10.1109/TMECH.2018.2855161.
X. Kuang, X. Huan, H. Xiao, and Y. Xu, “Simple modeling of a novel fuzzy memristor PID controller,” in Proc. of 3rd International Conference on Electronic Information Engineering and Computer (EIECT), 2023, https://doi.org/10.1109/EIECT60552.2023.10441986.
L. Chirco and S. Manservisi, “On the optimal control of stationary fluid–structure interaction systems,” Fluids, vol. 5, no. 3, p. 144, 2020, https://doi.org/10.3390/fluids5030144.
M. Wessberg, T. Vyhlídal, and T. Broström, “Humidity change rate control in intermittently heated historic buildings,” E3S Web of Conferences, vol. 172, p. 15004, 2020, https://doi.org/10.1051/e3sconf/202017215004.
V. N. Chernukha, S. M. Kastersky, and A. V. Suvorov, “Synthesis of pressure rate-of-change limits control in Pressurized Aircraft Cabin,” Science Intensive Technologies, 2022, https://doi.org/10.18127/j19998465-202206-05.
A. H. Akbar, A. Ma’arif, C. Rekik, A. J. Abougarair, and A. M. Mekonnen, “Implementing PID Control on Arduino Uno for Air Temperature Optimization”, Buletin Ilmiah Sarjana Teknik Elektro, vol. 6, no. 1, pp. 1–13, 2024, https://doi.org/10.12928/biste.v6i1.9725.
S. F. AL-Azzawi and M. M. Aziz, “Strategies of linear feedback control and its classification,” TELKOMNIKA (Telecommunication Computing Electronics and Control), vol. 17, no. 4, p. 1931, 2019, https://doi.org/10.12928/telkomnika.v17i4.10989.
M. Galina, G. E. Prasetyo, E. Sitompul, and A. Suhartomo, “Automatic door lock with hand cleaning and infra-red temperature detection system,” ELKOMIKA: Jurnal Teknik Energi Elektrik, Teknik Telekomunikasi, & Teknik Elektronika, vol. 10, no. 2, p. 364, 2022, https://doi.org/10.26760/elkomika.v10i2.364.
T. Tongskulroongruang and T. Jennawasin, “A comparative study of several ph control laws implemented to a smart hydroponics farm,” in Proc. of 22nd International Conference on Control, Automation and Systems (ICCAS), 2022, https://doi.org/10.23919/ICCAS55662.2022.10003913.
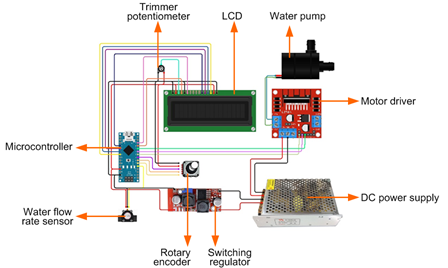
Published
How to Cite
Issue
Section
License
Copyright (c) 2024 Erwin Sitompul, Ridha Muhlita Putra, Hendra Tarigan, Arthur Silitonga, Iksan Bukhori

This work is licensed under a Creative Commons Attribution-ShareAlike 4.0 International License.
Authors who publish with this journal agree to the following terms:
- Authors retain copyright and grant the journal right of first publication with the work simultaneously licensed under a Creative Commons Attribution License that allows others to share the work with an acknowledgment of the work's authorship and initial publication in this journal.
- Authors are able to enter into separate, additional contractual arrangements for the non-exclusive distribution of the journal's published version of the work (e.g., post it to an institutional repository or publish it in a book), with an acknowledgment of its initial publication in this journal.
- Authors are permitted and encouraged to post their work online (e.g., in institutional repositories or on their website) prior to and during the submission process, as it can lead to productive exchanges, as well as earlier and greater citation of published work (See The Effect of Open Access).
This journal is licensed under a Creative Commons Attribution-ShareAlike 4.0 International License.