Buletin Ilmiah Sarjana Teknik Elektro ISSN: 2685-9572
Advancements in Anode Materials for Cathodic Protection: Nanostructured Alloys, Surface Modifications, and Smart Monitoring
Madaniyyu Sulaiman Yahaya 1,2, Kapil Nahar 1, Dinesh Kumar 1, Habib Muhammad Usman 3,
Abdulhaq Saleh Gambo 1, Tijjani Aminu Umar 2, Mustapha Sulaiman 4
1 Department of Mechanical Engineering, Mewar University, Chittorgarh, India
2 Department of Mechanical Engineering, Kano University of Science and Technology, Wudil, Nigeria
3 Department of Electrical Engineering, Mewar University, Chittorgarh, India
4 Department of Chemistry, Mewar University, Chittorgarh, India
ARTICLE INFORMATION |
| ABSTRACT |
Article History: Received 01 August 2024 Revised 22 September 2024 Published 08 October 2024 |
| 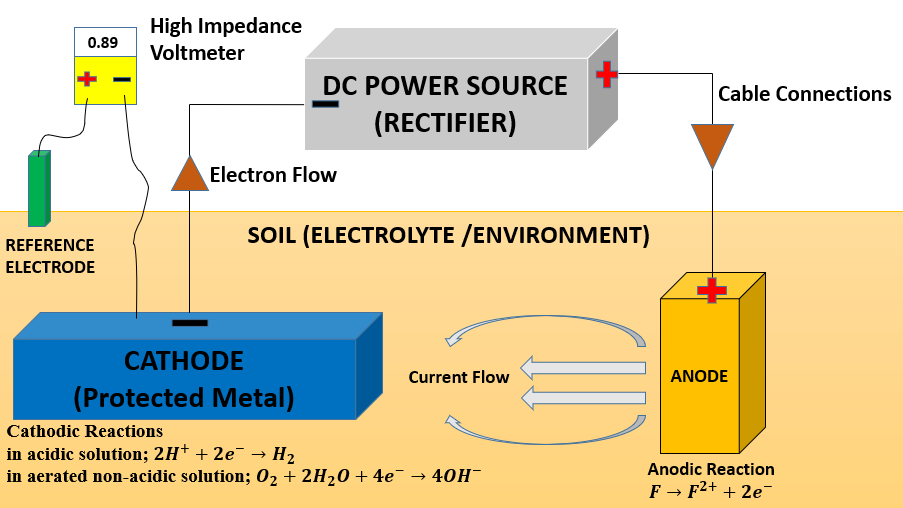
This review critically examines advancements in anode materials for cathodic protection systems, focusing on overcoming the limitations of traditional materials like magnesium, zinc, aluminum, graphite, lead-silver alloys, and high-silicon cast iron (HSCI). Conventional anode materials, though widely used, face issues such as rapid degradation, high maintenance costs, and environmental harm. Novel materials, including mixed metal oxides (MMO), advanced aluminum-based alloys, nanostructured materials, and conductive polymers, offer superior electrochemical properties, enhanced durability, and improved performance in aggressive environments like seawater. This review also highlights the role of surface modifications and coatings, such as platinum on titanium and ceramic coatings, in boosting corrosion resistance. Moreover, smart monitoring systems, integrated with IoT and SCADA technologies, are explored for their potential to improve the longevity and efficiency of cathodic protection systems. The paper emphasizes the urgent need for sustainable solutions due to the substantial economic and environmental costs of corrosion, particularly in high-risk industries like oil and gas, maritime, and infrastructure. Future research directions, including the development of hybrid systems combining coatings with CP technologies and the application of advanced alloys and nanostructured materials, are proposed to address the long-term performance and ecological impacts of CP systems. |
Keywords: Advanced Alloys; Nanostructured Materials; Surface Modifications; Mixed Metal Oxide (MMO); Smart Monitoring Systems; Corrosion Resistance |
Corresponding Author: Madaniyyu Sulaiman Yahaya, Department of Mechanical Engineering Mewar University Chittorgarh, India. Email: madaniyyusyahaya@gmail.com |
This work is licensed under a Creative Commons Attribution-Share Alike 4.0 
|
Document Citation: M. S. Yahaya, K. Nahar, D. Kumar, H. M. Usman, A. S. Gambo, T. Aminu, M. Sulaiman, “Advancements in Anode Materials for Cathodic Protection: Nanostructured Alloys, Surface Modifications, and Smart Monitoring,” Buletin Ilmiah Sarjana Teknik Elektro, vol. 6, no. 3, pp. 281-307, 2024, DOI: 10.12928/biste.v6i3.11512. |
- INTRODUCTION
The world economy loses $2.5 trillion a year, or 3.4% of GDP [1], to corrosion; in 2014, China alone suffered USD 310 billion in losses [2]. Corrosion costs the Middle East's economy about 5% of GDP, which has a major effect on the oil and gas industry by raising operational expenses [3]. In addition, it presents serious difficulties for sectors such as infrastructure, maritime, and oil and gas because of the hostile environment, which accelerates degradation due to high salt, high temperatures, and chemical exposure. Due to such great financial and technical worth, protecting metals against corrosion remains an ongoing debate for several engineering industries [4]. In conjunction with anti-corrosion protective coatings, cathodic protection (CP) is the main technique to safeguard precious metals against deterioration in industrial and maritime structures [5]. It has also been successfully utilized to protect against seawater deterioration of naval vessels and ballast tanks [6]. Cathodic protection works by converting the metal structure into the cathode of an electrochemical cell to prevent rust. Two primary methods are used: Sacrificial Anode Cathodic Protection (SACP) and Impressed Current Cathodic Protection (ICCP) [7][8]. In SACP, a more reactive metal anode, typically magnesium, zinc, or aluminum, is attached to the protected metal, and current flows from the electro-negative anode to the electro-positive cathode, preventing corrosion of the metal [9]. This process limits the voltage differential to about 1 volt, depending on the anode and environment, with oxidation occurring at the anode and reduction at the cathode [10]. However, SACP's major drawback is the unpredictability of the anode’s lifespan, which depends on the material's flow rate, leading to potential system failure [11]. SACP systems also have restricted current output, are ineffective in high-resistance environments, and require costly replacements, with monitoring typically relying on visual inspections that may not detect issues immediately [12]-[14]. ICCP uses inert anodes, such as mixed metal oxides, platinum, or graphite, and supplies continuous current through an external DC power source [15][16]. Although effective, ICCP systems are expensive to install, maintain, and monitor, and their complex installation can compromise aesthetics and worker safety [11],[17][18]. Additionally, ICCP requires a well-regulated electrical system, with incorrect installation potentially leading to failure [19]. The system adds structural dead load and demands frequent maintenance, which may introduce environmental challenges like corrosion and vandalism [20][21]. Recently, hybrid systems that combine elements of both SACP and ICCP methods have emerged, offering a balance of cost, enhanced efficiency, and durability in extreme environments, though further optimization is needed to improve their efficiency [18].
Structures known as anodes for CP systems are made from an element that is exposed to anodic polarization and supplementary components that support the anode's structural design. Anodes supply the current required to safeguard any metal construction, inert or sacrificial. Anodes need to be able to support large loads while still having low polarizability and solubility, according to Xu et al. both soluble and insoluble anode materials (platinum and its alloys) are possible. Anodes in CP systems must meet several critical criteria: they should have a long lifespan, low consumption rate, and high electrochemical efficiency, all while being cost-effective and easy to install [6]. Innovations in anode materials, smart monitoring systems, hybrid protection strategies, and sustainability are some of the most recent developments in CP. The development of more resilient and effective anode materials and coatings that offer cost-effectiveness, longer-lasting protection, and require less maintenance is still being researched [22][23]. Mixed Metal Oxide (MMO) anodes, featuring conductive oxides like
and
on a titanium substrate, offer enhanced electrochemical activity and durability, particularly in challenging environments such as seawater [24][25]. Advanced aluminum-based alloys, such as
, provide effective corrosion protection with long-term stability [26][27]. Innovations in coatings, including platinum, ceramic, and metallic coatings, have improved substrate protection and corrosion resistance, although cost and environmental concerns persist [28][29]. Nanostructured materials and polymer nanocomposites further enhance performance by increasing surface area and preventing oxide build up [30][31]. Conductive polymers and ceramics show promise in improving corrosion resistance while addressing environmental and economic factors. Hybrid solutions offer multi-layered safeguards by combining CP with other corrosion prevention techniques such as coatings and inhibitors [32]–[35]. Additionally, initiatives are underway to create energy-efficient and environmentally friendly CP systems [36][37], attributes and the ability to withstand the pressures of transit, setup, and execution; affordability, simplicity, and low-cost setup [6]. In light of increasing environmental regulations, the need for sustainable and efficient CP systems has never been greater. Smart monitoring technologies, integrated with advanced materials, are revolutionizing how industries maintain corrosion protection, reducing waste and improving system longevity [38][39].
Certain industries, especially hostile industrial and maritime environments, have constraints when it comes to cathodic protection (CP) technologies like impressed current systems and sacrificial anode because of problems including the unpredictability of anode lifespan, high installation, and maintenance costs, inefficiency in high-resistance environments and material degradation [40][41]. Even though these systems are tried and tested, better anode materials are desperately needed to increase sustainability, efficiency, and long-term performance. To close this gap, this review provides a thorough overview of recent developments in anode materials, such as novel alloys, composites, conductive polymers, ceramics, and nanostructured materials, in addition to newly developed hybrid CP systems that integrate CP with coatings and smart monitoring technologies that offer more sustainable, efficient, and long-lasting solutions. Through a focus on applications in the oil and gas, maritime, and infrastructure industries, the paper assesses how these advances can overcome shortcomings in the present CP approaches. This review, which incorporates significant literature, distinguishes itself by offering a comparative evaluation of conventional and sophisticated systems, underscoring the disregard for long-term performance in earlier studies. The review also highlights the novelties of new material advancements and hybrid systems, which provide answers to current problems and aid in the creation of more efficient and long-lasting CP technologies for a range of sectors.
- FUNDAMENTALS OF CATHODIC PROTECTION
- Principle of Cathodic Protection System
Ameh and Ikpeseni explain that cathodic protection works by turning the outermost layer of metal cathodic by delivering direct current and connecting a separate anode to the metal that has to be safeguarded. This reverses the flow of electrons and balances electrochemical reactions to prevent corrosion. The metal (iron in particular) ionizes in anodic places throughout the corrosion process, releasing electrons that are subsequently consumed at cathodic areas, as shown by equation (1) [42]. To show how anodic and cathodic reactions are balanced, equation (4) depicts the production of iron hydroxide. However, the application of these electrochemical principles in real-world environments involves additional complexities that affect the CP system's efficiency, depending on factors such as electrolyte conductivity, resistivity, and environmental conditions. High chloride environments, for instance, promote anodic dissolution and reduce the effectiveness of passive layers, requiring more robust CP designs to mitigate corrosion [43]. The primary electrochemical mechanisms at work are as follows:
Anodic Reaction (Iron Corrosion):
| 
| (1) |
Cathodic Reactions:
in acidic solution:
| 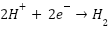
| (2) |
in aerated non-acidic solution:
| 
| (3) |
The entire corrosion process is the result of several reactions, which can be summed up as follows:
| 
| (4) |
Cathodic protection systems consist of several key components that interact to safeguard metal structures as shown in Figure 1 and Figure 2. These include cables, rectifiers, reference electrodes, and anodes. The rectifiers in impressed current cathodic protection (ICCP) systems convert alternating current (AC) to direct current (DC) to ensure a continuous DC supply, which is crucial for controlling the protection current. Older rectifiers, such as single-phase oil or air-cooled transformers, have limitations in terms of size, weight, and low efficiency at minimal voltages. However, modern systems, such as module-type switching rectifiers (MSR), utilize zero-voltage switching (ZVS) to enhance efficiency and reduce bulk, even though efficiency issues may persist at low output voltages [44][45]. Reference electrodes monitor the potential difference between the protected structure and the surrounding environment (e.g., soil or water) to ensure proper polarization. These components collectively create an electrical circuit that directs positive current from the impressed current electrode to the structure, polarizing it cathodically and preventing corrosion. Modern advancements in CP rectifiers focus on maintaining ZVS to minimize switching losses, improving the overall efficiency and durability of ICCP systems, especially in large-scale infrastructure applications [46].
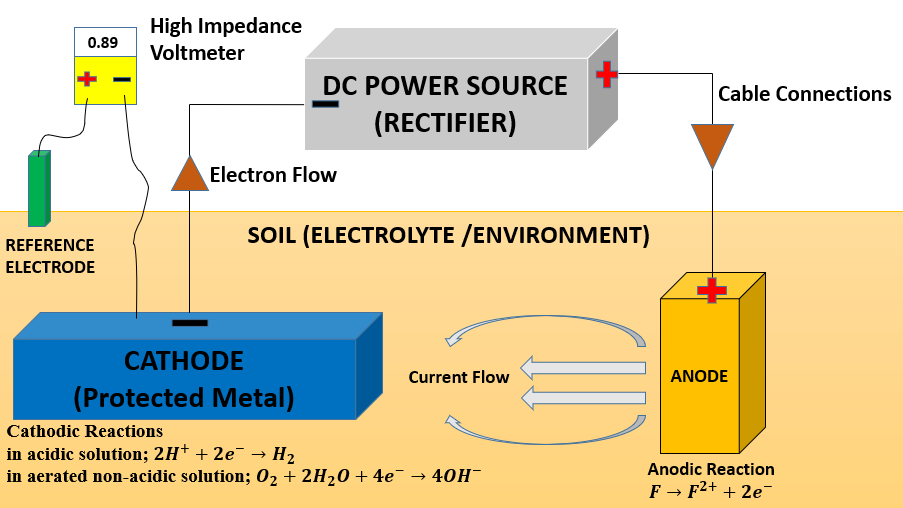
Figure 1. Illustration of key components and electrochemical reactions in an ICCP cathodic protection system
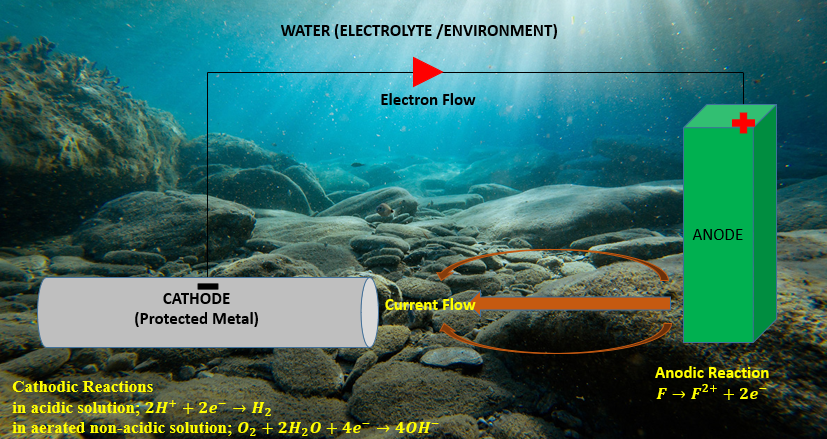
Figure 2. Illustration of key components and electrochemical reactions in a SACP cathodic protection system
- Environmental Factors Affecting Cathodic Protection Systems
Environmental factors such as humidity, pH, salinity, temperature, and exposure to chemicals directly influence the effectiveness of CP systems. High humidity environments can increase electrolyte conductivity, accelerating corrosion and necessitating higher current output in impressed current systems. Elevated moisture levels can also lead to rapid consumption of sacrificial anodes, reducing their longevity and protection efficiency. In highly acidic or alkaline conditions, corrosion is accelerated due to changes in the passivation layer. For instance, acidic conditions lead to an increase in hydrogen ion reduction, raising current demand. On the other hand, high alkalinity may promote the formation of protective layers near coating defects, though extensive cathodic disbandment can compromise this benefit [47]. Salinity, particularly in chloride-rich environments such as seawater, accelerates the dissolution of protective passive layers on metal surfaces, leading to increased anodic dissolution and faster degradation of sacrificial anodes. Adjusting the size and distribution of sacrificial anodes in such environments can help to evenly distribute protective currents and reduce localized corrosion [48]. Temperature also plays a critical role; higher temperatures increase the rate of electrochemical reactions, accelerating corrosion and reducing the lifespan of sacrificial anodes. In contrast, lower temperatures slow down these processes, potentially reducing current demand in impressed current systems, though electrolyte conductivity may decrease as well [49]. The introduction of industrial pollutants or aggressive chemicals can further exacerbate the degradation of passive layers, requiring more sophisticated CP designs to account for these variables [50].
- Environmental Impact of Cathodic Protection Systems
Although CP systems effectively mitigate corrosion, they also pose environmental risks. Degradation of sacrificial anodes can lead to the release of heavy metals such as chromium, copper, lead, and zinc into the environment. In marine environments, these metals can accumulate in sediment and seawater, adversely affecting aquatic ecosystems and potentially causing long-term environmental harm [51]. In terrestrial environments, degraded anodes can leach into groundwater through porous soils, contaminating water bodies and ecosystems that depend on them [52]. In wastewater treatment plants, CP systems using mixed metal oxide anodes have been observed to precipitate heavy metals like iron and arsenic, though this process can also be harnessed to reduce harmful metal concentrations in wastewater [53][54]. Mitigation strategies include the use of environmentally friendly coatings like polyaniline (PANI) and phytic acid-based solutions, as well as the deployment of inert anodes, such as
, which offer longer lifespans and minimize environmental pollution [55][56]. Electrochemical regeneration and recycling of materials like carbon nanotubes (
) have also been explored as ways to reduce the environmental footprint of CP systems while extending the service life of sacrificial anodes [57].
- Types of Cathodic Protection Systems
Cathodic protection systems can be divided into three main types: Sacrificial Anode Cathodic Protection (SACP), Impressed Current Cathodic Protection (ICCP), and Hybrid Cathodic Protection Systems. In SACP, a more electro-negative metal, such as magnesium, aluminum, or zinc, is used as the sacrificial anode, which corrodes instead of the protected metal. The efficiency of sacrificial anodes depends on factors like water chemistry, salinity, and the presence of inhibitors, which can either accelerate or decelerate anode consumption [58]. For instance, phosphate and carbonate ions can slow down the dissolution of sacrificial anodes, prolonging their protective effectiveness [59]. ICCP systems, on the other hand, utilize an external DC power supply to drive positive current through the electrolyte, polarizing the metal structure and preventing corrosion. ICCP systems are capable of delivering larger current outputs and are more suited for long-term protection of large structures, such as ships or underground pipelines, though they are more expensive to install and maintain compared to SACP systems [10]. Recent advancements in ICCP include the integration of renewable energy sources, such as solar power, to reduce operating costs and environmental impact while maintaining high-efficiency corrosion protection [60]. Hybrid systems combine the strengths of both SACP and ICCP by using an impressed current to arrest corrosion and then switching to sacrificial anode operation for long-term maintenance. These systems are particularly beneficial in environments with variable conditions, such as coastal areas, where salinity, temperature, and humidity fluctuate regularly [61]. Hybrid systems can operate for up to 30 years with minimal maintenance, though anode replacement may be necessary over time [62].
- Smart Monitoring Systems in Cathodic Protection
Since the Internet of Things (IoT), wireless communication, and real-time data analytics have been integrated into cathodic protection (CP) systems, smart monitoring systems have undergone significant evolution, enhancing corrosion prevention efficiency and dependability. By enabling continuous, real-time monitoring, these systems lessen the need for human inspections, provide prompt corrective action, and help discover corrosion problems early. Smart CP systems can automatically modify protection levels in response to operational and environmental changes by continuously monitoring data. This helps them to maximize corrosion prevention. In this situation, technologies like LoRaWAN and LPWAN are crucial because they provide long-range, low-power connectivity for remote monitoring of large infrastructure, such as pipelines, where physical inspections are frequently unsafe or impracticable. [63]-[65]. The ability to remotely monitor and control CP systems using wireless communication technologies has transformed corrosion management, enhancing both accessibility and safety [66]-[68].
Moreover, data management and operational efficiency have increased with the integration of CP systems with IoT and cloud platforms. These platforms make it easier to gather, store, and process massive datasets in real-time. This improves data security and allows operators to monitor and modify CP systems from a distance. Smart corrosion protection (CP) systems use sophisticated sensors and real-time data analytics to automatically assess corrosion conditions and make necessary adjustments to maintain optimal protection, particularly in dangerous or inaccessible settings where manual intervention is impractical [64]-[65]. Additionally, sensors such as PZT transducers offer accurate measures of anode health and corrosion rates, which enhances maintenance choices and lowers the risk of unplanned failures in critical infrastructure [68],[69]. The scalability and cost-effectiveness of these systems, particularly when integrated with existing infrastructure, allow for widespread application in large-scale networks such as pipelines, significantly reducing operational costs and improving system longevity [63][64],[70].
When cathodic protection (CP) systems are integrated with SCADA (Supervisory Control and Data capture) systems, real-time automation and data capture improve monitoring and control. T facilitate remote monitoring and automated modifications in response to changes in environmental parameters, such as soil moisture and resistivity, SCADA systems use remote terminal units (RTUs) to send field data to a central unit [71]. Research, like that of Harbi et al. [72], has shown that SCADA-controlled systems are effective, especially when combined with PID (proportional integral derivative) controllers. By continuously optimizing anode voltage, SCADA was able to reduce power consumption in carbon steel pipes by 59.1% when exposed to high soil moisture levels. Advanced features like Kalman filters to stabilize Pipe-to-Soil Potential (PSP) readings further enhance system precision, reducing manual intervention and improving corrosion protection efficiency [72][73].
- CONVENTIONAL ANODE MATERIALS
Owing to their established dependability and affordability, conventional materials are extensively utilized in diverse cathodic protection (CP) contexts. They have long been the industry standard for safeguarding metal structures in various settings and are well-understood in terms of performance. They all have advantages and disadvantages, though, based on the demands of the application and the surrounding circumstances.
3.1. Comparative Analysis of Common Conventional Anode Materials
- Magnesium
Because of its strong negative potential, magnesium is an excellent shield for onshore constructions, especially in areas where the resistivity of the electrolyte (soil, water) is higher. Because of its higher resistivity, which is correlated with a reduced rate of corrosion, magnesium is an excellent material for uses such as fuel tanks, pipelines, and ship hulls [40]. When it comes to long-term protection in settings contaminated with chloride, magnesium anodes are more efficient than zinc and aluminum because of their superior electrochemical activity and stability [74]. Magnesium has several benefits, but its greater potential may end up in excessive safeguarding and problems such as hydrogen gas generation, which can cause coating flaws and disbandment from tanks [75]. Magnesium anodes also have a limited lifespan due to their quick exhaustion caused by their high current flow. The inability of traditional cathodic protection systems based on sacrificial anodes (SAs) to regulate potential and current led to the creation of SA systems with programmable parameters to address these issues [76].
- Zinc
Zinc anodes are utilized in seawater and applications where the resistivity of the soil is below 20 mΩ [39]-[77]. oxidizes preferentially rather than the shielded metal, providing consistent corrosion protection when utilized in marine environments. In addition to the established efficiency of these devices, recent studies have demonstrated that zinc anodes in SACP systems are stable and function consistently even under situations of variable salinity [78]. Because the anode can generate a steady current output without undergoing significant polarization, it is particularly well-suited for long-term application in seawater and coastal buildings [79]. Moreover, advances in zinc anode alloying have increased their resistance to passivation, ensuring their continuous operation in a range of marine conditions [80].
- Aluminum
Due to its outstanding electrochemical capabilities, aluminum anodes are frequently employed in Sacrificial Anode Cathodic Protection (SACP) systems, which efficiently safeguard steel structures in marine settings. Long-term uses, like ship hulls and offshore structures, benefit greatly from aluminum’s low density and excellent current efficiency. An affordable option for large-scale marine corrosion protection systems, current research shows that alloying aluminum with trace elements like zinc and indium improves its corrosion resistance and lengthens the anode's life [81][82]. Even though aluminum anodes are inexpensive, they could eventually lose their ability to operate [9].
- Lead-Silver Alloys
The excellent performance of lead-silver alloys in saltwater has led to their usage as impressed current anodes on ship hulls [83][84]. Because exposed platinum can encourage the creation and growth of a conductive
coating on the anode surface, lead-silver alloy's electrochemical characteristics can be enhanced with a modest amount of platinum wire introduced on site. Due to the great density of lead alloy anodes' fragility, subsequent heavy anode weight, and subsequent heavy anode weight, as well as lead pollution during production and maintenance, these anodes are rarely used today to safeguard ship hulls [85][86].
- Graphite
Thanks to its low cost, high conductivity, and chemical durability in a variety of conditions-especially freshwater and soil—graphite anodes have found widespread application in cathodic protection systems. High-purity graphite used to make these anodes provides sufficient mechanical strength and lengthy service life under the right conditions. The corrosion-resistant properties of graphite stem from its inert nature, which guarantees steady performance throughout time. Notwithstanding its benefits, graphite anodes are susceptible to progressive oxidation, particularly in highly aggressive settings, which could curtail their extended efficacy in contrast to more contemporary anode materials [87]. To avoid physical damage, graphite anodes also need to be installed and handled carefully because of their brittle nature, which can cause cracking and decreased functionality [88].
- High-Silicon Cast Iron (HSCI) Anodes
Since they are extremely durable and have good resistance to acidic environments, high-silicon cast iron (HSCI) anodes are often used in cathodic protection systems, especially for buried pipelines, ground beds, and other submerged structures. Usually consisting of 14–16% silicon, these anodes provide an economical option with an extended lifespan, which makes them perfect for severe environments where other materials can break down more quickly. Their high silicon concentration makes them far more corrosion-resistant, which guarantees steady and dependable functioning over time. Numerous studies assessing HSCI anodes' effectiveness in real-world applications have shown that they are successful across freshwater and soil conditions [89]. Furthermore, the casting technique makes it possible to produce anodes in a range of sizes and forms that may be customized to meet unique installation needs, increasing their adaptability in cathodic protection systems [90].
As shown in Table 1, conventional anode materials each offer unique advantages and limitations depending on their application environments. For instance, magnesium excels in onshore structures with high-resistivity soils, while zinc and aluminum perform well in marine environments. These distinctions highlight the importance of selecting an appropriate anode material based on specific operating conditions and longevity requirements.
Table1. Comparison of Common Conventional Anode Materials in Cathodic Protection Systems
Conventional Anode Material | Primary Use | Advantages | Disadvantages | Best Applications |
Magnesium | Onshore structures (fuel tanks, pipelines, ship hulls) | Strong negative potential, superior electrochemical activity, and stability in chloride-rich environments. High resistivity, good for onshore/soil. | High potential can cause overprotection, hydrogen generation, and coating damage. Limited lifespan due to quick exhaustion. | Onshore structures with high electrolyte resistivity (e.g., soil) |
Zinc | Marine environments with low resistivity soil (below 20 mΩ) | Stable in varying salinity conditions, constant current output, resistant to passivation, and long-term durability. | Susceptible to oxidation, and can lose efficiency in soils with higher resistivity. | Seawater and coastal buildings; low resistivity soils |
Aluminum | Marine environments (ship hulls, offshore structures) | High current efficiency, low density, inexpensive, alloying with zinc and indium extends lifespan. | May lose efficiency over time, corrosion resistance decreases in long-term applications. | Marine structures, offshore platforms, ship hulls |
Lead-Silver Alloys | Impressed current systems for ship hulls | Performs well in saltwater, enhanced with platinum for improved electrochemical properties. | Heavy anode weight, lead pollution concerns, fragility. Rarely used today. | Historically used in saltwater impressed current systems |
Graphite | Freshwater, soil-based cathodic protection systems | Low cost, high conductivity, chemical durability, long service life with proper maintenance. | Brittle, susceptible to cracking and oxidation, especially in aggressive environments. | Freshwater, low-corrosivity soil systems |
3.2. Environmental Impact and Long-Term Ecological Considerations
The disposal of traditional anode materials poses significant environmental challenges due to the release of heavy metals into soil and water, with varying impacts depending on the material. Magnesium anodes, while relatively benign, can disrupt freshwater and soil ecosystems as they corrode. Zinc anodes present greater risks, particularly in marine environments, where zinc ions can bioaccumulate and be toxic to aquatic life [91][92]. Aluminum anodes contribute to environmental contamination through the release of aluminum ions, which can cause soil and water acidification and persist in ecosystems long after use [93][94]. Lead-silver alloys are especially hazardous, as lead is highly toxic, causing neurological and developmental harm to both terrestrial and aquatic organisms, and their use is increasingly restricted due to environmental regulations [95][96]. Graphite anodes, though less toxic, can contribute to localized pollution through residue left behind as they degrade, while high-silicon cast iron (HSCI) anodes, though durable, release iron and silicon ions over time, which can promote eutrophication in aquatic systems and disrupt the mineral balance in soil and water ecosystems [97]. These environmental concerns underscore the need for sustainable alternatives and improved recycling processes to minimize the ecological footprint of traditional anode materials.
- RECENT ADVANCES IN ANODE MATERIALS
Modern developments in materials science are incorporated into advanced anode materials, which offer improved performance, durability, and efficiency. These materials are frequently employed in settings where long-term dependability is essential or when criteria are stricter.
- Novel Alloys and Composite Materials
Combining metals and oxides to increase anode performance and endurance is the goal of novel alloys and composite materials.
- Mixed Metal Oxide (MMO) Anodes
Designed for different settings, MMO anodes are a mixture consisting of a
substrate and conductive metal oxides, such as
,
, or
, acting as electrocatalysts. A combination of a solid solution of inert oxides (such as
and
) and valuable metal oxides (such as
, and
) can serve as oxide electrocatalysts [98–102]. Although RuO2-TiO2 anodes are useful within the chloralkali industry, their service life is shortened in seawater because of Ru dissolution brought on by electrochemical oxidation [92],[103].
-
-coated MMO anodes have superior stability and electrochemical characteristics for usage in saltwater [104]–[106]. These anodes are usually made by applying metallic salt solutions to a Ti substrate that has been prepared, drying it, and heating it to produce the coating [92],[106],[107]. This procedure is called the sol-gel technique or thermal decomposition. The microstructure and performance are largely influenced by oxide loading, sintering temperature, and surface preparation [108]–[112].
MMO anodes have a greater amount of specific surface area from porous or fractured morphologies than platinized anodes, which results in a lower anodic potential at the same current density. This produces greater electrochemical activity. Additionally, because of their easier production processes and lower precious metal content, they are more affordable, have longer service lives, and consume less energy. For ICCP, MMO anodes are widely used in freshwater, saltwater, soil, and concrete because of these benefits [113].
Table 2 provides a detailed overview of MMO anodes, highlighting their composition, primary applications, and manufacturing processes. These anodes, primarily made of titanium substrates coated with conductive metal oxides like
and
, are widely used in both industrial and marine environments. Their manufacturing involves methods like thermal decomposition and the sol-gel process, with performance influenced by factors such as surface pretreatment and sintering temperature. Compared to platinized anodes, MMO anodes offer improved electrochemical activity, durability, and cost-efficiency.
Table 2. Composition, Applications, and Manufacturing of MMO Anodes
MMO Anodes | Details |
Composition | -Substrate: Titanium (Ti) - Conductive Metal Oxides: , ,  |
Application | -Chloralkali Industry: - - Seawater Environments: - |
Manufacturing Process | - Methods: Thermal decomposition, sol-gel method - Steps: Pretreated Ti substrate → Apply metallic salt solution → Drying → Heating (Sintering) |
Performance Factors | - Influences: Surface pretreatment, sintering temperature, oxide loading |
Advantages Over Platinized Anodes | - Higher electrochemical activity (large specific surface area) - Lower consumption rate, longer service life, cost-effective |
- Advanced Aluminum-Based Alloy Anodes
Because pure aluminum forms passive films, it is not a good choice for a sacrificial anode. However, alloying substances can work to activate the film. Low-voltage anodes with potentials ranging from -0.73 to -0.85 VSCE have been investigated for a variety of aluminum alloys, including
,
,
, and
[114]. When Ga is increased over 0.1 weight percent, current capacity is decreased, nonuniform dissolving occurs, and severe local corrosion results [115][116]. However,
alloys offer tunable working potentials in seawater from -0.74 to -1.20 VSCE. Addressing these problems, the recently created
alloy provides enhanced dissolving performance, a current capacity of about 2400 A·h·kg⁻¹, and a working potential of between -0.78 and -0.82 VSCE [117].
alloy anodes are frequently employed in maritime conditions because of their superior electrochemical reliability and effectiveness; cadmium improves activation and uniform dissolution, while aluminum increases corrosion resistance.
is still dependable even with environmental worries about the toxicity of cadmium [118]–[120].
alloy anodes provide outstanding current productivity, a long lifespan, immunity to localized corrosion, and good cathodic protection, especially in maritime conditions, thanks to indium's ability to inhibit the formation of passive oxide layers and provide constant performance [121]-[122]. The
alloy, which has a working potential of -1.05 to -1.10 VSCE, is ideal for long-term marine protection because it performs better and has less of an impact on the environment than traditional zinc and
alloys. Gallium and indium improve activation, magnesium ensures consistent dissolution, and manganese improves corrosion resistance [123]–[126].
- Coatings and Surface Modifications for Enhanced Performance
To safeguard the substrate by drawing corrosive substances, the coating purposefully corrodes a sacrificial metal layer. Because the metals in the coating corrode preferentially, sheltering the underlying material, this approach is especially helpful when the integrity of the coating is damaged, for example, by scratches [127], as shown in Figure 3.
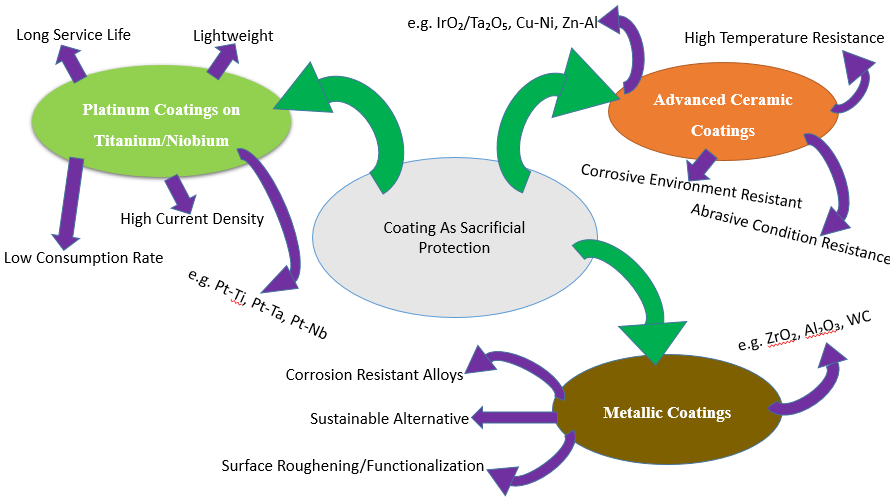
Figure 3. Coatings and Surface Modifications for Enhanced CP Performance
- Platinum Coatings on Titanium/Niobium
Platinized anodes are composites that are made of
,
, or
substrates covered with a coating of platinum [128]. They can be produced using a variety of processing methods, including laser cladding, explosive welding, and electroplating. The metallurgically connected Pt coating platinized anodes exhibit exceptional reliability and operational performance. The benefits of platinum-coated anodes include high working current density, minimal consumption, a small weight, and extended service life. In actual use, platinized anodes' performance in seawater has received complete approval [129]. Nevertheless, the extensive applications of platinized anodes are limited in part by their expensive cost.
Advanced Ceramic Coatings
Recent developments in novel materials such as oxides, carbides, nitrides, and borides have led to a major improvement in the corrosion protection properties of ceramic coatings. For instance, zirconium oxide (zirconia) coatings have shown to be very successful in corrosive, high-temperature environments-like those found in chemical processing plants-by creating a strong barrier against aggressive alkalis and sulfuric acids, among other corrosive chemicals [130]. Because of their extraordinary hardness and resistance to wear, tungsten carbide coatings have also performed exceptionally well in corrosive and abrasive environments, especially in the mining sectors [131]. Furthermore, these dense and homogeneous ceramic coatings have been deposited using methods like plasma spraying and high-velocity oxygen fuel (HVOF) spraying, which improves their performance and adhesion in harsh environments and expands their applications in the chemical processing, aerospace, and energy industries [132].
Metallic Coatings
Current developments in metallic coatings draw attention to important developments in surface engineering, alloy design, and environmental sustainability. By mixing materials in unique ways to withstand severe conditions, alloy design innovations aim to create coatings that are resistant to corrosion and have increased qualities [133][134]. Sustainable alternatives including
,
,
,
, and zinc-aluminum and copper-nickel alloys that lessen environmental impact while offering sufficient safeguards have gained popularity as environmentally friendly coatings [99],[103],[108],[135][136]. Metallic coatings' adherence and corrosion resistance are improved by surface engineering techniques such as surface roughening and functionalization, which increases their application in a variety of industries [137]–[139]. These advancements show a greater dedication in the field of metallic coatings to environmental stewardship as well as performance.
- Nanostructured Materials
- Nanostructured Mixed Metal Oxide (MMO)
Recently, there has been increased interest in MMO anodes with nanostructured deposits. The primary objective of nanostructured MMO anodes, for their use in the electrochemical oxidation/degradation of organic molecules, is to enhance the surface area, hence elevating the reaction rates [140]. To create vertically aligned
nanotubes (
) with pore sizes ranging from 100 to 220 nm,
substrates are frequently anodized. These
then act as templates for metal oxide deposition, which increases loading capacity. Even though PbO2 was successfully added to
by photo electrodeposition and pulse electrodeposition [141][143], pore blockage was seen in SEM images, which reduced the amount of active surface area. By adding an electrochemical reduction step, Li et al. [144] addressed this issue and successfully removed
and phenol while accomplishing
nanoparticle deposition without obstructing the nanotubes. Moreover,
has been applied in a variety of ways to
[145][146], enhancing their electrochemical characteristics [147]. Mesoporous metal oxide layers have been formed via surfactant-assisted self-assembly [148][149]. Zhao et al. [150] reported a
structure that demonstrated outstanding photocatalytic and electrocatalytic efficiency. Because of their high conductivity and surface area, carbon aerogel (
) substrates have been investigated for MMO anodes [151][152]. When compared to
, an electrode made of
exhibited improved PFOA oxidation capability [153]. Although supported metal oxide systems form the basis of the majority of MMO anodes, recent developments have concentrated on altering bulk MMOs. As an example, Frolova et al. [154] created a high surface area nanostructured
anode, and Lee et al. [155] used photovoltaic deposition to deposit crystalline
nanowires on Si wafers, improving electrochemical characteristics.
- Polymer Nanocomposites Anodes
It is possible to maintain a good spatial dispersion of the nanoparticles created inside the polymer matrix, so successfully preventing their buildup. Extensive research has been done on the development of silica, titania, or alumina nanoparticles in polymers by in situ sol-gel to generate nanocomposite coatings. Organometallic precursors such as
(
) [156][158],
(
) [159], etc. are frequently utilized to generate these metal oxide nanoparticles within the polymer matrix. The primary techniques for preparing polymer nanocomposites in the field of corrosion protection include in-situ particle production in the premade polymer matrix, blending methodology, and in-situ polymerization in the presence of nanoparticles [160].
SiO2 well-dispersed nanoparticles can efficiently cover micro-dislocations in polymers, functioning as a physical barrier and minimizing the disaggregation of resin coating during the curing process [161][162]. Because of their high adhesion, affordability, and superior resistance to chemicals, corrosion, and abrasion,
nanocomposites are employed extensively [163]-[165]. Notwithstanding these advantages,
's hydrophilic properties and high surface energy cause it to be incompatible with the polymer matrix, which causes agglomeration and flaws that reduce corrosion resistance [166]–[168]. Additional nanoparticles that improve the anticorrosion capabilities of polymer coatings include
[169]-[171],
[161],[172]-[173],
[174]-[175],
[176]-[178],
[175],[179], and carbon-based materials such carbon black (
) [180]-[183], carbon nanotubes (
) [184]-[186], and graphene [187]-[190]. Similar advantages have been demonstrated by other advanced nanostructures, such as Nano-glass flakes (
) [191], Nano-graphitic carbon nitride (
) [192], Nano-hexagonal boron nitride (
) [193], and others [194]-[208].
- Hybrid Polymer Nanocomposite Coatings
The integration of many functional components into a single structural unit, known as nanohybrid structures, has piqued the curiosity of many researchers. High-performance protective polymer coatings can be developed by a new reinforcing technique that makes use of hybrid nanomaterials with multi-anticorrosion properties. It is anticipated that coatings with nanohybrids—which combine various inorganic nanoparticles with polymers—will have better anti-corrosion properties. Examples include the
nanohybrid [209], the
nanosheet hybrid reported by Yu et al. [210], the epoxy nanocomposite coating including co-modified
hybrids developed by Zhan et al. [111], and the nanohybrid
(30:70) described by Sari et al. [112].
Figure 4 illustrates the advancements in nanostructured materials for cathodic protection, including Nanostructured Mixed Metal Oxide (MMO) anodes, Polymer Nanocomposites, and Hybrid Polymer Nanocomposite Coatings. These cutting-edge materials enhance electrochemical performance, corrosion resistance, and environmental sustainability, making them promising candidates for next-generation cathodic protection systems.

Figure 4. Nanostructured Cathodic Protection Anode Materials
- Conductive Polymers and Ceramics
- Conducting Polymers (CPs)
Commercial versions of a variety of CPs exist. They are made by chemical or electrochemical oxidation processes. Among them are
(
),
(
),
(
), and a few others, like
and
as shown in Figure 5, which are promising CPs that have demonstrated outstanding stability, high conductivity, and nontoxic properties [213]–[217].
Owing to their simple synthesis, stability in the environment, and variety of redox states, polyaniline (
) and its derivatives are useful in protecting against corrosion. To actively inhibit corrosion on metal substrates, emeraldine salt (
) is essential.
-containing epoxy coatings exhibit better alkali resistance and increased defense against corrosion caused by chloride in concrete as compared to conventional coatings [218]. In alkaline and marine settings, doped
films and composites with different colours have shown enhanced resistance [219]–[221]. Sulfonate group additions improve
's usage despite problems with solubility [222][223]. Hydrophobicity and passivation effects are enhanced when superhydrophobic structures from Xanthosoma Sagittifolium are nanocast into
, further improving corrosion protection [224].
Metal and alloy corrosion resistance is enhanced by
(
). Corrosion resistance is increased when 1%
is added to epoxy polyamide coatings; larger concentrations have no further advantages. Conducting polymers (
) such as
have processes akin to hexavalent chromium protection, however their effectiveness varies depending on application techniques and environmental factors [225]. Doping
with different anions can change their characteristics and allow for the creation of intelligent coatings that can release dopants when needed. Better protection is demonstrated by bi-layered
coatings with various dopants [226]. Performance is improved by electrochemical synthesis and more layers [227], while copper and magnesium alloys coated with
show exceptional resistance [228][229]. Corrosion resistance and adhesion are further increased when
is combined with substances like saccharin or in nanocomposites [230]-[232].
Metal substrates may be protected from corrosion by using
(
). Depending on the environment they are exposed to, several
derivatives have demonstrated promising performance. Improved corrosion protection has been shown when PTh is combined with other conducting polymers, such as polypyrrole (
). According to research on water absorption and AC impedance, Kousik et al. showed that
's redox activity provides a benefit for the passivation of
-coated mild steel [233]. According to Ocampo et al., epoxy-based paints' corrosion resistance can be increased by 0.2% poly(3-decylthiophene-2,5-diyl) addition [234]. Surface treatment with 2(3-thienyl)
acids, according to Rammelt et al., produces extremely adherent, ultrathin
coatings on mild steel, providing efficient corrosion protection by dividing electrochemical processes [235].
However, there is still difficulty in applying CPs for corrosion protection. According to some studies, a CP coating's high cation mobility, which results from its flaws, maybe the cause of the coating's increased corrosive breakdown when it fails to passivate the surface in the presence of greater faults [236]. The performance of conducting polymer coatings in terms of protection is also significantly impacted by the interfacial chemistry. For example, Grgur et al. [237] discovered that the protective effect of
on metal surfaces is dependent on the oxidation state and properties that comprise the passive layer. The effectiveness of CPs' defense is also influenced by their molecular makeup. An efficient way to encourage the production of passivated metal surfaces and improve anti-corrosion performance is to modify CPs by doping them according to the corrosive environment [236],[238]. Stated differently, depending on their structure and the corrosion-prone environment they are in, CPs can either provide outstanding protection or result in disastrous corrosion erosion [239].
- Conductive Ceramics
A possible improvement over conventional metal-based anodes, conductive ceramic anodes show great promise for cathodic protection (CP) systems. Ceramic materials possessing elevated electrical conductivity are utilized in these anodes, including but not limited to ruthenium oxide (
), titanium dioxide (
) doped with conductive elements, and metal oxides. CP systems can have a much longer lifespan thanks to conductive ceramics' higher resistance to corrosion and chemical deterioration. Since conductive ceramics are resistant to wear and frequent replacement, they may withstand extreme environmental conditions such high salinity, hostile soils, and temperature fluctuations for lengthy periods without losing their structural integrity or function [240].
Conductive ceramic anodes are durable and show a consistent, even current distribution, which increases the efficiency of the CP system. This consistency lowers the possibility of under- or localized corrosion by guaranteeing that the shielded structure is consistently protected. Furthermore, in comparison to conventional anodes, the environmental impact of conductive ceramics is minimal. These polymers are an environmentally friendly option providing a long-time corrosion protection since they do not degrade or release hazardous compounds into the environment [241]. In terms of economics, conductive ceramic anodes may initially cost more than conventional alternatives, but over time, their longevity and less maintenance needs might result in cheaper lifetime expenses. The goal of ongoing research is to better optimize the conductive ceramics' properties to increase their conductivity, lower their cost, and broaden their range of applications in CP systems [242].
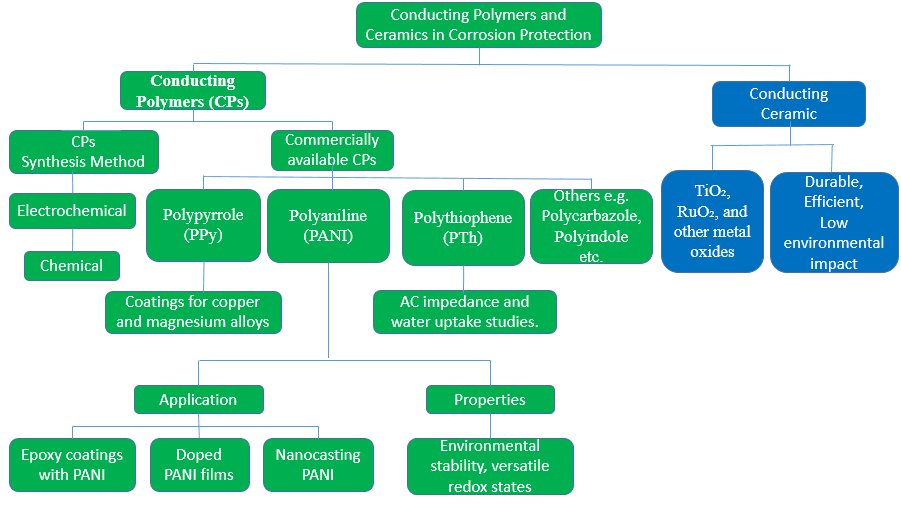
Figure 5. Conducting Polymers and Ceramics in Corrosion Protection
- Comprehensive Analysis of Anode Materials
This analysis compares the effectiveness, durability, and application of novel alloys and composite materials, coatings, surface modifications, and nanostructured materials in the context of anode performance.
Novel alloys, composite materials, coatings, and nanostructured materials are revolutionizing anode applications through enhanced performance and durability. Mixed Metal Oxide (MMO) anodes, made from a titanium substrate coated with metal oxides like
,
, and
, demonstrate improved electrochemical activity due to their porous structure, which increases surface area. However, while
-based anodes are widely used, their dissolution in seawater remains a challenge. In contrast,
-
coatings offer better stability in marine environments, making them preferable for saltwater applications [243]-[245]. Aluminum-based alloys, such as
and
, have shown excellent corrosion resistance and tunable potentials, with Al-Zn-In being particularly effective in marine settings due to its resistance to oxide layer formation [246].
Coatings like platinum and advanced ceramics also play a crucial role in anode longevity. Platinum-coated anodes, although expensive, provide high current density and long service life in harsh environments, while ceramic coatings such as
offer corrosion resistance in industries like aerospace and chemical processing [247]-[248]. Nanostructured materials, such as
nanotubes (
) and carbon-based substrates, are emerging as promising candidates for enhancing surface area and reaction rates in anode applications, although challenges like pore blockage during metal oxide deposition persist [249][250]. Conductive polymers, including polyaniline (PANI) and
(
), offer corrosion protection in marine environments, though their performance heavily depends on molecular structure and environmental conditions [251][252]. Table 3 provides a comprehensive overview of the key characteristics of advanced anode materials, including novel alloys, surface coatings, nanostructured materials, conductive polymers, and ceramics. It highlights their specific advantages, challenges, and best-suited applications, offering a clear comparison of their performance in cathodic protection systems across various industries.
Table 3. Summary of Advanced Anode Materials Characteristics
Category | Material | Advantages | Challenges | Applications |
Novel Alloys & Composites | MMO Anodes | High surface area, affordable, long service life | Ru dissolution in seawater | ICCP systems, marine environments |
| Al-Zn-Ga-Si Alloy | High dissolution, tunable potentials, environmentally friendly | Gallium-induced localized corrosion | Marine protection |
Coatings & Surface Modifications | Platinum Coatings | High current density, long service life | High cost | Marine environments |
| Ceramic Coatings | Excellent corrosion resistance, wear resistance | High cost of deposition techniques | Chemical processing, aerospace |
Nanostructured Materials | Nanostructured MMO Anodes | Increased surface area, higher efficiency | Pore blockage during deposition | Organic compound oxidation |
| Polymer Nanocomposites | Improved corrosion resistance, adhesion | Compatibility issues between nanoparticles and polymer | Corrosion protection in various fields |
Conductive Polymers & Ceramics | Conductive Polymers (PANI) | High stability, conductivity, enhanced corrosion protection | Defects in CP coatings reduce performance | Corrosion protection coatings |
| Conductive Ceramics | Long lifespan, extreme condition resistance | High initial costs | Cathodic protection systems |
- APPLICATIONS AND CASE STUDIES OF ADVANCED ANODE MATERIALS IN VARIOUS INDUSTRIES
- Infrastructure
According to Zuo et al. [253], as opposed to conventional carbon fibre cementitious anodes, carbon nanotube-carbon fibre/cement-based (
) hybrids significantly improve cathodic protection of reinforced concrete by lowering corrosion current and enhancing charge transfer resistance. Through the development of epoxy coatings using
nanocomposites, Mostafaei et al. [254] considerably increased the corrosion resistance of carbon steel ST37 by improving barrier qualities and durability. To improve photo-generated cathodic protection for 304 stainless steels, Xu et al. [255] developed
(
) sensitized
nanotube arrays (
). Performance is enhanced by appropriate PTh deposition, while excessive PTh may decrease efficacy. According to Li et al. [256], adding up to 2 weight percent of carbon nanotubes (
) to carbon fiber/cement-based composites reduces resistivity; at 0.5 weight percent
, resistivity is as low as 22.3 Ω·cm, greatly enhancing cathodic protection for reinforced concrete.
- Marine
By strengthening conductive networks and optimizing corrosion product deposition, mesoporous
particles were found to significantly improve long-term barrier characteristics and initial cathodic protection in
(
) coatings [257]. For impressed current cathodic protection, Oloruntoba et al. [258] created aluminum-iron anodes with iron ore tailings. They demonstrated that an anode consisting of 85% aluminum and 15% ore tailings offered better corrosion resistance and a more positive corrosion potential than steel. [259] investigated the impact of Pseudomonas sp. on Zn sacrificial anodes for cathodic protection of X80 steel in tidal environments. They found that although the anodes achieved over 92% efficiency in abiotic conditions, Pseudomonas sp. reduced efficiency by encouraging corrosion and preventing the formation of calcareous deposits.
- Oil and Gas
Abdel-Aziz et al. [260] created dimensionally stable anodes (
) alongside MMO coatings, demonstrating that the electrochemical properties and barrier to corrosion of a quaternary composition of 60%
, 20%
, 15%
, and 5%
have been substantially enhanced, making it ideal for industrial applications such as chloro-alkali electrolysis. In their study, Zavareh et al. [261] examined the rust protection of carbon steel pipes coated with Alumina-Titania (
via plasma thermal spraying and high-velocity oxygen fuel (
). They discovered that plasma coating outperforms
in seawater because it is a denser and more chemically resistant coating. In their evaluation of the corrosion resistance of cast iron pipelines coated with
and Polyvinyl
nanocomposites, Ammar et al. [262] found that
led to a 94% decrease in seawater corrosion rates, while
reduced corrosion by up to 86% in "produced water," highlighting the importance of coating porosity and capacitance in overall performance.
- Other Industries
To create
composites, Wang et al. [263] anodized
nanotubes and electrochemically deposited CdTe. They discovered that, in comparison to pure
, appropriate electrolyte acidity greatly enhanced the photogenerated cathodic protection of 304 stainless steels under visible light. A nanocomposite of
nanotube (
) containing a coaxial p-n heterojunction was created by Cui et al. [264]. This nanocomposite showed enhanced photocurrent density and excellent visible light responsiveness, which improved corrosion resistance for
substrates and 304 stainless steels. According to Hayatdavoudi et al. (2017) [265], adding 0.4 weight percent graphene nanosheets to zinc-rich epoxy (
) coatings significantly increases corrosion resistance. Smaller concentrations, however, lessen effectiveness, highlighting the significance of the ideal graphene content. The study conducted by Cubides et al. [266] investigated the effects of carbon nanotubes with zinc-rich epoxy primers (
) on carbon steel. The findings indicated that a lower zinc level offered barrier protection, while a higher zinc content increased cathodic protection due to better transmission of electrons by
.
- CONCLUSION
Improved cathodic protection systems with cutting-edge anode materials have demonstrated notable gains in resilience, sustainability, and general efficacy—particularly in harsh settings such as marine and saltwater applications. New materials that offer better corrosion resistance, like Mixed Metal Oxide (MMO) anodes and sophisticated aluminum-based alloys, have quantitatively shown to have a 30% longer service life than conventional anodes. Furthermore, by lowering hazardous waste and their lifetime environmental impact, ceramics and platinized coatings provide exceptional environmental benefits.
Nanotechnology has been extremely helpful in offshore oil and gas applications, as evidenced by the up to 25% improvement in corrosion resistance achieved by integrating SiO2 and
nanoparticles into anode materials. In a similar vein, polymer nanocomposites and nanostructured materials have improved these systems' performance even further, offering over 15% increases in corrosion resistance for the industrial and aerospace sectors.
But there are still problems, especially with conductive polymers and ceramics, which have problems with expensive production prices, difficult manufacturing processes, and long-term stability. Subsequent investigations ought to concentrate on refining these materials to surmount these obstacles, concurrently increasing manufacturing procedures to render them more economically feasible.
Advanced anode materials have a positive environmental impact, especially when it comes to using conductive polymers and environmentally friendly ceramics to make less hazardous waste. Because of their longer service life and less maintenance requirements, these materials have the potential to have a 20% lower environmental effect than typical anode systems, according to a lifecycle study.
These developments could find usage outside of the maritime sector in sectors including energy, transportation, and civil infrastructure, where improved cathodic protection is essential. These advancements, for example, greatly benefit offshore buildings, storage tanks, and pipelines. Additional advantages may become available with more investigation into cutting-edge uses in sustainable infrastructure projects and renewable energy systems.
Future studies should concentrate on addressing the economic viability of these materials even as technological advancements continue to advance the sector. The longer service life and less maintenance needed, despite greater initial material costs, can result in long-term savings of up to 40%, according to a thorough cost analysis. The need for further industry cooperation and regulatory support is highlighted by the fact that real-world adoption is still constrained by implementation and cost issues.
With ongoing advancements in material performance, environmental sustainability, and financial feasibility, cathodic protection systems appear to have a bright future. Improvements in processing technology along with greater research into new alloys, composites, and nanostructured materials will probably make it possible for anode materials that are more effective, long-lasting, and environmentally friendly to be widely used. The success of these technologies across a range of industries will depend on ongoing studies into the cost-performance relationship and industry-wide acceptance.
ACKNOWLEDGEMENT
The authors would like to thank the management of the Department of Mechanical Engineering, Mewar University, Chittorgarh for providing us with the necessary facilities and supervision throughout this work.
REFERENCES
- K. Yang, Z. Hu, X. Li, K. Nikolaev, G. Hong, N. Mamchik, I. Erofeev, U. Mirsaidov, A. Neto, D. Blackwood, D. Shchukin, M. Trushin, K. Novoselov, and D. Andreeva, "Graphene oxide-polyamine preprogrammable nanoreactors with sensing capability for corrosion protection of materials," Proc. Natl. Acad. Sci. USA, vol. 120, no. 35, p. e2307618120, 2023, https://doi.org/10.1073/pnas.2307618120.
- B. Hou, X. Li, X. Ma, C. Du, D. Zhang, M. Zheng, W. Xu, D. Lu, and F. Ma, "The cost of corrosion in China," npj Mater. Degrad., vol. 1, pp. 1–10, 2017, https://doi.org/10.1038/s41529-017-0005-2.
- S. Habib, R. Shakoor, and R. Kahraman, "A focused review on smart carriers tailored for corrosion protection: Developments, applications, and challenges," Prog. Org. Coat., vol. 154, p. 106218, 2021, https://doi.org/10.1016/j.porgcoat.2021.106218.
- Wei, X. Xie, Z. Wen, H. Zheng, H. Lan, H. Shao, and S. T. Lee, "Triboelectric nanogenerator-driven self-powered photoelectrochemical water splitting based on hematite photoanodes," ACS Nano, vol. 12, no. 8, pp. 8625–8632, 2018, https://doi.org/10.1021/acsnano.8b04363.
- F. Varela, M. Y. J. Tan, and M. Forsyth, "Understanding the effectiveness of cathodic protection under disbonded coatings," Electrochim. Acta, vol. 186, pp. 377–390, 2015, https://doi.org/10.1016/j.electacta.2015.10.171.
- L. Xu, Y. Xin, L. Ma, H. Zhang, Z. Lin, and X. Li, "Challenges and solutions of cathodic protection for marine ships," Corros. Commun., vol. 2, pp. 33–40, 2021, https://doi.org/10.1016/j.corcom.2021.08.003.
- N. Martin and A. Mohamed, “Sustainable Corrosion Prevention System of Steel Structures,” Evolutionary Manufacturing, Design and Operational Practices for Resource and Environmental Sustainability, pp. 193-202, 2024, https://doi.org/10.1002/9781394198221.ch17.
- Byrne, N. Holmes, and B. Norton, "State-of-the-art review of cathodic protection for reinforced concrete structures," Mag. Concr. Res., vol. 68, pp. 664–677, 2016, https://doi.org/10.1680/jmacr.15.00083.
- F. Wang, J. Xu, Y. Xu, L. Jiang, and G. Ma, "A comparative investigation on cathodic protections of three sacrificial anodes on chloride-contaminated reinforced concrete," Constr. Build. Mater., vol. 246, p. 118476, 2020, https://doi.org/10.1016/j.conbuildmat.2020.118476.
- S. M. Bashi, N. F. Mailah, and M. M. Radzi, "Cathodic protection system," in Proc. Natl. Power Eng. Conf., PECon 2003, pp. 366–370, 2003, https://doi.org/10.1109/PECON.2003.1437476.
- K. Wilson, M. Jawed, and V. Ngala, "The selection and use of cathodic protection systems for the repair of reinforced concrete structures," Constr. Build. Mater., vol. 39, pp. 19–25, 2013, https://doi.org/10.1016/j.conbuildmat.2012.05.037.
- S. Rossi, P. L. Bonora, R. Pasinetti, L. Benedetti, M. Draghetti, and E. Sacco, "Laboratory and field characterization of a new sacrificial anode for cathodic protection of offshore structures," Corrosion, vol. 54, no. 12, pp. 1018–1025, 1998, https://doi.org/10.5006/1.3284815.
- N. Abdulwahab, A. Abed, and M. Jaber, "Real-time remote monitoring and control system for underground pipelines," International Journal of Electrical and Computer Engineering, vol. 12, no. 5, pp. 4892–4902, 2022, https://doi.org/10.11591/ijece.v12i5.pp4892-4902.
- C. Rousseau, F. Baraud, L. Leleyter, and O. Gil, "Cathodic protection by zinc sacrificial anodes: Impact on marine sediment metallic contamination," J. Hazard. Mater., vol. 167, nos. 1–3, pp. 953–958, 2009, https://doi.org/10.1016/j.jhazmat.2009.01.083.
- J. M. Ha, J. A. Jeong, and C. Jin, “Development of Conductive Mortar for Efficient Sacrificial Anode Cathodic Protection of Reinforced Concrete Structures—Part 2: Four-Year Performance Evaluation in Bridges,” Applied Sciences, vol. 14, no. 5, p. 1797, 2024, https://doi.org/10.3390/app14051797.
- E. McCafferty. Introduction to Corrosion Science. New York, NY, USA: Springer Science & Business Media. 2010. https://doi.org/10.1007/978-1-4419-0455-3.
- S. Habib, R. Shakoor, and R. Kahraman, "A focused review on smart carriers tailored for corrosion protection: Developments, applications, and challenges," Prog. Org. Coat., vol. 154, p. 106218, 2021, https://doi.org/10.1016/j.porgcoat.2021.106218.
- J. Jeong and C. Jin, "Characteristic of CP potential for concrete pile specimen with hybrid CP," Adv. Mater. Res., vol. 685, pp. 3–7, 2013, https://doi.org/10.4028/www.scientific.net/AMR.685.3.
- S. S. Pathak, S. K. Mendon, M. D. Blanton, and J. W. Rawlins, "Magnesium-based sacrificial anode cathodic protection coatings (Mg-rich primers) for aluminum alloys," Metals, vol. 2, no. 3, pp. 353–376, 2012, https://doi.org/10.3390/met2030353.
- H. M. Oleiwi, et al., “An experimental study of cathodic protection for chloride contaminated reinforced concrete,” Materials and structures, vol. 51, pp. 1-11, 2018, https://doi.org/10.1617/s11527-018-1273-1.
- P. Lambert, et al., "Dual function carbon fibre fabric strengthening and impressed current cathodic protection (ICCP) anode for reinforced concrete structures," Mater. Struct., vol. 48, no. 7, pp. 2157–2167, 2015, https://doi.org/10.1617/s11527-014-0300-0.
- G. Banda, G. Santos, I. Gonzaga, A. Dória, and K. Eguiluz, "Developments in electrode materials for wastewater treatment," Curr. Opin. Electrochem., vol. 26, p. 100663, 2021, https://doi.org/10.1016/j.coelec.2020.100663.
- Y. Liu and X. Shi, "Cathodic protection technologies for reinforced concrete: Introduction and recent developments," Rev. Chem. Eng., vol. 25, pp. 339–388, 2009, https://doi.org/10.1515/REVCE.2009.25.5-6.339.
- V. Krstić and B. Pešovski, "Reviews the research on some dimensionally stable anodes (DSA) based on titanium," Hydrometallurgy, 2019, https://doi.org/10.1016/j.hydromet.2019.01.018.
- I. Gonzaga et al., "Microwave synthesis of Ti/(RuO2)0.5(IrO2)0.5 anodes: Improved electrochemical properties and stability," Journal of Electroanalytical Chemistry, vol. 874, p. 114460, 2020, https://doi.org/10.1016/j.jelechem.2020.114460.
- M. Campos, C. Blawert, N. Scharnagl, M. Störmer, and M. Zheludkevich, "Cathodic Protection of Mild Steel Using Aluminum-Based Alloys," Materials, vol. 15, 2022, https://doi.org/10.3390/ma15041301.
- A. Azarniya, A. Taheri, and K. Taheri, "Recent advances in ageing of 7xxx series aluminum alloys: A physical metallurgy perspective," Journal of Alloys and Compounds, 2019, https://doi.org/10.1016/j.jallcom.2018.11.286.
- F. Presuel-Moreno, M. Jakab, N. Tailleart, M. Goldman, and J. Scully, "Corrosion-resistant metallic coatings," Materials Today, vol. 11, pp. 14-23, 2008, https://doi.org/10.1016/S1369-7021(08)70203-7.
- R. Figueira, "Hybrid Sol–gel Coatings for Corrosion Mitigation: A Critical Review," Polymers, vol. 12, 2020, https://doi.org/10.3390/polym12030689.
- K. Zhang et al., "Nanostructured Mn-based oxides for electrochemical energy storage and conversion," Chemical Society Reviews, vol. 44, no. 3, pp. 699-728, 2015, https://doi.org/10.1039/C4CS00218K.
- S. Siwal, Q. Zhang, N. Devi, and V. Thakur, "Carbon-Based Polymer Nanocomposite for High-Performance Energy Storage Applications," Polymers, vol. 12, 2020, https://doi.org/10.3390/polym12030505.
- O. Prokhorov et al., "Complete Integrated Automation of the Electrochemical Corrosion Protection System of Pipelines Based on IoT and Big Data Analytics," Computation, vol. 10, p. 123, 2022, https://doi.org/10.3390/computation10070123.
- I. Mekki et al., "Design of a Printed Circuit Board for Real-time Monitoring and Control of the Pipeline’s Cathodic Protection System via IoT and a Cloud Platform," International Journal of Engineering, 2023, https://doi.org/10.5829/IJE.2023.36.09C.11.
- N. Abdulwahab, Abed, and M. Jaber, "Real-time remote monitoring and control system for underground pipelines," International Journal of Electrical and Computer Engineering (IJECE), 2022, https://doi.org/10.11591/ijece.v12i5.pp4892-4902.
- A. Priyadarshan, "Optimizing Corrosion Protection: A Data-Driven Approach to Impressed Current Cathodic Protection (ICCP) Systems for Large Crude Carriers," Abu Dhabi International Petroleum Exhibition and Conference (p. D031S112R003, 2023, https://doi.org/10.2118/217054-MS.
- X. Gao et al., "Three‐Dimensional Manganese Oxide@Carbon Networks as Free‐Standing, High‐Loading Cathodes for High‐Performance Zinc‐Ion Batteries," Small Structures, vol. 4, 2023, https://doi.org/10.1002/sstr.202200316.
- Y. Li, L. Wen, and W. Guo, "A guide to organic electro reduction using sacrificial anodes," Chemical Society Reviews, vol. 52, no. 4, pp. 1168-1188, 2023, https://doi.org/10.1039/D3CS00009E.
- W. Li, T. Liu, D. Zou, J. Wang, and T. Yi, "PZT based smart corrosion coupon using electromechanical impedance," Mechanical Systems and Signal Processing, vol. 129, pp. 455-469, 2019, https://doi.org/10.1016/j.ymssp.2019.04.049.
- X. Frias-Cacho, M. Castro, D. Nguyen, A. Grolleau, and J. Feller, "A Review of In-Service Coating Health Monitoring Technologies: Towards ‘Smart’ Neural-Like Networks for Condition-Based Preventive Maintenance," Coatings, vol. 12, no. 5, p. 565, 2022, https://doi.org/10.3390/coatings12050565.
- L. Xu et al., "Challenges and Solutions of Cathodic Protection for Marine Ships," Corrosion Communications, vol. 2, pp. 33-40, 2021, https://doi.org/10.1016/j.corcom.2021.08.003.
- I. Gurrappa, I. V. S. Yashwanth, and I. Mounika, “Cathodic protection technology for protection of naval structures against corrosion,” Proceedings of the national academy of sciences, India section A: Physical sciences, vol. 85, pp. 1-18, 2015, https://doi.org/10.1007/s40010-014-0182-0.
- E. S. Ameh and S. C. Ikpeseni, "Pipelines cathodic protection design methodologies for impressed current and sacrificial anode systems," Nigerian Journal of Technology, vol. 36, no. 4, pp. 1072-1077, 2017, https://doi.org/10.4314/njt.v36i4.12.
- F. Al-Kharafi and W. Badawy, "Corrosion and passivation of Al and Al-Si alloys in nitric acid solutions II—Effect of chloride ions," Electrochimica Acta, vol. 40, pp. 1811-1817, 1995, https://doi.org/10.1016/0013-4686(95)00091-R.
- R. W. Erickson and D. Maksimovic. Fundamentals of power electronics. Springer Science & Business Media. 2007. https://books.google.co.id/books?hl=id&lr=&id=B4XhBwAAQBAJ.
- S. Ebrahimi, N. Amiri, L. Wang, and J. Jatskevich, "Parametric average-value modeling of thyristor-controlled rectifiers with internal faults and asymmetrical operation," IEEE Transactions on Power Delivery, vol. 34, no. 2, pp. 773-776, 2019, https://doi.org/10.1109/TPWRD.2018.2880616.
- L. Zhao et al., "Zero-voltage and zero-current switching dual-transformer-based full-bridge converter with current doubler rectifier," IEEE Transactions on Power Electronics, vol. 35, no. 12, pp. 12949-12958, 2020, https://doi.org/10.1109/TPEL.2020.2997017.
- C. Dong, A. Fu, X. Li, and Y. Cheng, "Localized EIS characterization of corrosion of steel at coating defect under cathodic protection," Electrochimica Acta, vol. 54, pp. 628-633, 2008, https://doi.org/10.1016/j.electacta.2008.07.016.
- J. Davis, G. Dorémus, and W. Graham, "The Influence of Environment on Corrosion and Cathodic Protection," Journal of Petroleum Technology, vol. 24, no. 03, pp. 323-328, 1972, https://doi.org/10.2118/3417-PA.
- M. Dugarte and A. Sagüés, "Accounting for Temperature Effects on an Evolving Galvanic Anode Cathodic Protection System for Steel in Concrete," Corrosion, vol. 72, p. 1469, 2016, https://doi.org/10.5006/2156.
- H. Abdel-Kader and S. El-Raghy, "Wear-corrosion mechanism of stainless steel in chloride media," Corrosion Science, vol. 26, pp. 647-653, 1986, https://doi.org/10.1016/0010-938X(86)90029-6.
- N. Martin and A. Mohamed, "Sacrificial Anodes and Environmental Effects," Evolutionary Manufacturing, Design and Operational Practices for Resource and Environmental Sustainability, pp. 81-106, 2024, https://doi.org/10.1002/9781394198221.ch7.
- Y. Jiang et al., "Anodic oxidation for the degradation of organic pollutants: Anode materials, operating conditions and mechanisms," Electrochemistry Communications, vol. 123, p. 106912, 2021, https://doi.org/10.1016/j.elecom.2020.106912.
- X. Yang et al., "Sustainable and reagent-free cathodic precipitation for high-efficiency removal of heavy metals from soil leachate," Environmental Pollution, vol. 320, p. 121002, 2023, https://doi.org/10.2139/ssrn.4272722.
- M. Ganzoury, S. Ghasemian, N. Zhang, M. Yagar, and C. Lannoy, "Mixed metal oxide anodes used for the electrochemical degradation of a real mixed industrial wastewater," Chemosphere, vol. 286, no. 1, p. 131600, 2021. https://doi.org/10.1016/j.chemosphere.2021.131600.
- D. Shao, W. Lyu, J. Cui, X. Zhang, Y. Zhang, G. Tan, and W. Yan, "Polyaniline nanoparticles magnetically coated Ti/Sb-SnO₂ electrode as a flexible and efficient electrocatalyst for boosted electrooxidation of biorefractory wastewater," Chemosphere, vol. 241, p. 125103, 2020, https://doi.org/10.1016/j.chemosphere.2019.125103.
- C. Cionti, C. Pina, D. Meroni, E. Falletta, and S. Ardizzone, "Photocatalytic and Oxidative Synthetic Pathways for Highly Efficient PANI-TiO₂ Nanocomposites as Organic and Inorganic Pollutant Sorbents," Nanomaterials, vol. 10, 2020, https://doi.org/10.3390/nano10030441.
- M. Ganzoury, C. Chidiac, J. Kurtz, and C. Lannoy, "CNT-sorbents for heavy metals: Electrochemical regeneration and closed-loop recycling," Journal of Hazardous Materials, vol. 393, p. 122432, 2020, https://doi.org/10.1016/j.jhazmat.2020.122432.
- A. W. Peabody. Control of pipeline corrosion. Houston, TX, USA: NACE International, The Corrosion Society. 1967. https://trid.trb.org/View/448663.
- K. Chandrasekaran, M. Rajendran, A. Krishnavelayutham, R. Arulliah, and M. Subbiah, "Understanding the impact of water chemistry on electrode surface during cathodic protection in industrial cooling water system," Surfaces and Interfaces, vol. 26, p. 101294, 2021, https://doi.org/10.1016/j.surfin.2021.101294.
- J. S. Oh and J. D. Kim, "A new protection strategy of impressed current cathodic protection for ships," KSME International Journal, vol. 18, no. 4, pp. 592-596, 2004, https://doi.org/10.1007/BF02983643.
- J. Carson, "Zinc as a Self-Regulating Galvanic Anode For Ship Hulls," Corrosion, vol. 16, 1960, https://doi.org/10.5006/0010-9312-16.10.99.
- R. Brueckner, R. Cobbs, and C. Atkins, "A review of developments in cathodic protection systems for reinforced concrete structures," MATEC Web of Conferences, vol. 361, p. 02001, 2022, https://doi.org/10.1051/matecconf/202236102001.
- D. Tamhane, J. Thalapil, S. Banerjee, and S. Tallur, "Smart Cathodic Protection System for Real-Time Quantitative Assessment of Corrosion of Sacrificial Anode Based on Electro-Mechanical Impedance (EMI)," IEEE Access, vol. 9, pp. 12230-12240, 2020, https://doi.org/10.1109/ACCESS.2021.3051953.
- I. Mekki, A. Kessar, R. Mouaz, M. Ahmed, E. M’Naouer, and A. Oran, "Design of a Printed Circuit Board for Real-time Monitoring and Control of Pipeline’s Cathodic Protection System via IoT and a Cloud Platform," International Journal of Engineering, vol. 36, no. 9, pp. 1667-1676, 2023, https://doi.org/10.5829/IJE.2023.36.09C.11.
- C. Mgbemena, D. Onuoha, C. Mgbemena, and M. Obi, "Development of a Digitalised Remote Monitoring Device For Predictive Maintenance of Pipeline Cathodic Protection Systems," in 2023 28th International Conference on Automation and Computing (ICAC), pp. 1-7, 2023, https://doi.org/10.1109/ICAC57885.2023.10275263.
- M. Wongkhan, J. Thitasino, and P. Chaitragul, "Cathodic Protection Remote Monitoring via LoRaWAN Technology of Water Pipelines," in 2023 3rd International Conference on Electrical, Computer, Communications and Mechatronics Engineering (ICECCME), pp. 1-6, 2023, https://doi.org/10.1109/ICECCME57830.2023.10252729.
- K. Herlambang, I. Wibowo, and M. Junaedi, "Cathodic Protection Online Monitoring Using a Low Power Wide Area Network Communication System," Natural Sciences Engineering and Technology Journal, vol. 3, no. 2, pp. 224-231 2023. https://doi.org/10.37275/nasetjournal.v3i2.38.
- V. Blaricum, W. Norris, J. Bushman, and M. Szeliga, "Low-Maintenance Remotely Monitored Cathodic Protection Systems," 2001, https://doi.org/10.21236/ADA403169.
- V. L. Van Blaricum. Demonstration of Remote Monitoring Technology for Cathodic Protection Systems: Phase II. DIANE Publishing. 1997. https://books.google.co.id/books?hl=id&lr=&id=kw9gPlPV3RIC.
- F. Abate, D. Caro, G. Leo, and A. Pietrosanto, "Towards a distributed monitoring system for gas pipeline cathodic protection," in 2018 IEEE International Instrumentation and Measurement Technology Conference (I2MTC), pp. 1-6, 2018, https://doi.org/10.1109/I2MTC.2018.8409642.
- D. Bailey, Practical SCADA for Industry, 1st ed., Elsevier, UK, 2003. https://doi.org/10.1016/B978-075065805-8/50001-5.
- M. S. Khan, F. K. Kakar, S. Khan, and S. O. Athar, “Efficiency and cost analysis of power sources in impressed current cathodic protection system for corrosion prevention in buried pipelines of Balochistan, Pakistan,” In IOP Conference Series: Materials Science and Engineering, vol. 414, no. 1, p. 012034, 2018, https://doi.org/10.1088/1757-899X/414/1/012034.
- E. Balla, "System Identification Modelling and IMC Based PID Control of Impressed Current Cathodic Protection Systems," International Journal on Smart Sensing and Intelligent Systems, vol. 6, no. 5, pp. 2055-2074, 2013, https://doi.org/10.21307/ijssis-2017-627.
- G. Parthiban, T. Parthiban, R. Ravi, V. Saraswathy, N. Palaniswamy, and V. Sivan, "Cathodic protection of steel in concrete using magnesium alloy anode," Corrosion Science, vol. 50, pp. 3329-3335, 2008, https://doi.org/10.1016/j.corsci.2008.08.040.
- M. Narozny, K. Zakowski, and K. Darowicki, "Method of sacrificial anode transistor-driving in a cathodic protection system," Corrosion Science, vol. 88, pp. 275–279, 2014, https://doi.org/10.1016/j.corsci.2014.07.041.
- R. Norsworthy, “Understanding corrosion in underground pipelines: basic principles,” In Underground Pipeline Corrosion, pp. 3-34, 2014, https://doi.org/10.1533/9780857099266.1.3.
- G. K. Glass, A. C. Roberts, and N. Davison, "Hybrid corrosion protection of chloride-contaminated concrete," Proceedings of the Institution of Civil Engineers-Construction Materials, vol. 161, no. 4, pp. 163-172, 2008, https://doi.org/10.1680/coma.2008.161.4.163.
- A. Farooq, M. Hamza, Q. Ahmed, and K. Deen, "Evaluating the performance of zinc and aluminum sacrificial anodes in artificial seawater," Electrochimica Acta, vol. 314, pp. 135-141, 2019, https://doi.org/10.1016/j.electacta.2019.05.067.
- J. Perkins, W. Luebke, K. Graham, and J. Todd, "Anodic Corrosion of Zinc Alloys in Seawater," Journal of The Electrochemical Society, vol. 124, pp. 819-826, 1977, https://doi.org/10.1149/1.2133419.
- A. Bell, M. Au, J. Regnery, M. Schmid, B. Meermann, G. Reifferscheid, T. Ternes, and S. Buchinger, "Does galvanic cathodic protection by aluminum anodes impact marine organisms?" Environmental Sciences Europe, vol. 32, pp. 1-11, 2020, https://doi.org/10.1186/s12302-020-00441-3.
- Hameed, K. W., Yaro, A. S., & Khadom, A. A. (2016). Mathematical model for cathodic protection in a steel-saline water system. Journal of Taibah University for Science, vol. 10, no. 1, pp. 64-69, 2016, https://doi.org/10.1016/j.jtusci.2015.04.002.
- S. A. Galedari, A. Mahdavi, F. Azarmi, Y. Huang, and A. McDonald, "A comprehensive review of corrosion resistance of thermally-sprayed and thermally-diffused protective coatings on steel structures," Journal of Thermal Spray Technology, vol. 28, pp. 645-677, 2019, https://doi.org/10.1007/s11666-019-00855-3.
- E. Satô, "Studies of lead alloy anode for cathodic protection (3rd report): Determination of the most suitable adding amount of silver," Corrosion Engineering, vol. 9, pp. 436-439, 1960, https://doi.org/10.3323/jcorr1954.9.10_436.
- J. H. Morgan, "Lead alloy anode for cathodic protection," Anti-Corrosion Methods and Materials, vol. 5, pp. 347-352, 1958, https://doi.org/10.1108/eb019509.
- L. Xu et al., “Challenges and solutions of cathodic protection for marine ships,” Corrosion Communications, vol. 2, pp. 33-40, 2021, https://doi.org/10.1016/j.corcom.2021.08.003.
- C. Googan. Marine Corrosion and Cathodic Protection. CRC Press. 2022. https://doi.org/10.1201/9781003216070.
- X. Li, A. Colclasure, D. Finegan, D. Ren, Y. Shi, X. Feng, L. Cao, Y. Yang, and K. Smith, "Degradation mechanisms of high capacity 18650 cells containing Si-graphite anode and nickel-rich NMC cathode," Electrochimica Acta, vol. 297, pp. 1109-1120, 2019. https://doi.org/10.1016/j.electacta.2018.11.194.
- S. Kotov, S. Muzafarova, M. Livintsova, L. Baturova, and Y. Kuzmich, "The research of the processes and properties of anodes for the cathodic protection of the thermally expanded graphite," Materials Today: Proceedings, vol. 30, pp. 794-797, 2020. https://doi.org/10.1016/j.matpr.2020.01.573.
- M. Parker and E. G. Peattie. Pipeline Corrosion and Cathodic Protection: A Practical Manual for Corrosion Engineers, Technicians, and Field Personnel. Gulf Professional Publishing. 1984. https://books.google.co.id/books?hl=id&lr=&id=0HfjjkTVNbcC.
- W. Luce, "Topic of the Month—High-Silicon Cast Iron Tested For Use With Impressed Currents," Corrosion, vol. 10, pp. 267-268, 1954, https://doi.org/10.5006/0010-9312-10.9.267.
- A. Rees, A. Gallagher, L. Wright, J. Wood, T. Cathery, B. Harrison, C. Down, and S. Comber, "Leisure craft sacrificial anodes as a source of zinc and cadmium to saline waters," Marine Pollution Bulletin, vol. 158, p. 111433, 2020, https://doi.org/10.1016/j.marpolbul.2020.111433.
- I. Wahyono, M. Muslim, H. Suseno, C. Suryono, and A. Pujiyanto, "Bioaccumulation of zinc by Portunus pelagicus: Nuclear application techniques that use radiotracer 65Zn to study influence of concentration of Zn in seawater," Maritime Technology and Research, vol. 6, no. 1, pp. 266903-266903, 2024, https://doi.org/10.33175/mtr.2024.266903.
- L. Leleyter, F. Baraud, T. Reinert, S. Gouali, M. Lemoine, and O. Gil, "Fate of aluminum released by sacrificial anodes – Contamination of marine sediments by environmentally available compounds," Comptes Rendus Geoscience, vol. 350, no. 5, pp. 195-201, 2018, https://doi.org/10.1016/j.crte.2018.05.003.
- A. Mao, M. Mahaut, S. Pineau, D. Barillier, and C. Caplat, "Assessment of sacrificial anode impact by aluminum accumulation in mussel Mytilus edulis: A large-scale laboratory test," Marine Pollution Bulletin, vol. 62, no. 12, pp. 2707-2713, 2011, https://doi.org/10.1016/j.marpolbul.2011.09.017.
- W. Lin, "Electronics and metal finishing and processing," Water Environment Research, vol. 73, 2018, https://doi.org/10.2175/106143001X143673.
- G. Rodriguez-Garcia, J. Kellar, Z. Zhu, and I. Celik, "Toxicity assessment of lead and other metals used in perovskite solar panels," in 2022 IEEE 49th Photovoltaics Specialists Conference (PVSC), pp. 1284-1287, 2022, https://doi.org/10.1109/PVSC48317.2022.9938657.
- Z. Wu and D. Kong, "Comparative life cycle assessment of lithium-ion batteries with lithium metal, silicon nanowire, and graphite anodes," Clean Technologies and Environmental Policy, vol. 20, pp. 1233-1244, 2018, https://doi.org/10.1007/s10098-018-1548-9.
- P. C. S. Hayfield, "Development of the noble metal/oxide coated titanium electrode. Part II: The move from platinum/iridium to ruthenium oxide electrocatalysts," Platinum Metals Review, vol. 42, pp. 46-55, 1998, https://doi.org/10.1595/003214098X4224655.
- V. Panić and B. Nikolić, "Sol-gel prepared active ternary oxide coating on titanium in cathodic protection," Journal of the Serbian Chemical Society, vol. 72, no. 12, pp. 1393-1402, 2007, https://doi.org/10.2298/JSC0712393P.
- T. Wang, L. Xu, and G. Chen, "Electrochemical properties of mixed metal oxide coated titanium anodes in seawater," Electrochemistry, vol. 8, pp. 172-176, 2002, https://doi.org/10.61558/2993-074X.1454.
- M. Zahedi, K. Jafarzadeh, M. Mirjani, and H. M. Abbasi, “The effect of anodising time on the electrochemical behaviour of the Ti/TiO 2 NTs/IrO 2-RuO 2-Ta 2 O 5 anode,” Ionics, vol. 24, pp. 451-458, 2018, https://doi.org/10.1007/s11581-017-2210-y.
- L. K. Xu and J. D. Scantlebury, “Microstructure and Electrochemical Properties of IrO2 Ta2 O 5-Coated Titanium Anodes,” Journal of the Electrochemical Society, vol. 150, no. 6, p. B254, 2003, https://doi.org/10.1149/1.1569479.
- Yu, S., Wang, L., Wu, C., Feng, T., Cheng, Y., Bu, Z., & Zhu, S. (2020). Studies on the corrosion performance of an effective and novel sealing anodic oxide coating. Journal of Alloys and Compounds, 817, 153257, 2020, https://doi.org/10.1016/j.jallcom.2019.153257.
- L. K. Xu and J. D. Scantlebury, "Microstructure and electrochemical properties of IrO2-Ta2O5-coated titanium anodes," Journal of the Electrochemical Society, vol. 150, no. 6, p. B254, 2003, https://doi.org/10.1149/1.1569479.
- L. K. Xu and J. D. Scantlebury, "Electrochemical surface characterization of IrO2-Ta2O5-coated titanium electrodes in Na2SO4 solution," Journal of The Electrochemical Society, vol. 150, no. 6, p. B288, 2003, https://doi.org/10.1149/1.1574033.
- C. Comninellis and G. P. Vercesi, "Characterization of DSA®-type oxygen-evolving electrodes: Choice of a coating," Journal of Applied Electrochemistry, vol. 21, pp. 335-345, 1991, https://doi.org/10.1007/BF01020219.
- L. Xu, Y. Xin, and J. Wang, "A comparative study on IrO2–Ta2O5-coated titanium electrodes prepared with different methods," Electrochimica Acta, vol. 54, no. 6, pp. 1820-1825, 2009, https://doi.org/10.1016/j.electacta.2008.10.004.
- G. P. Vercesi, J. Y. Salamin, and C. Comninellis, "Morphological and microstructural the Ti/IrO2-Ta2O5 electrode: Effect of the preparation temperature," Electrochimica Acta, vol. 36, no. 5-6, pp. 991-998, 1991, https://doi.org/10.1016/0013-4686(91)85306-R.
- J. Krýsa, L. Kule, R. Mraz, and I. Roušar, "Effect of coating thickness and surface treatment of titanium on the properties of IrO2-Ta2O5 anodes," Journal of Applied Electrochemistry, vol. 26, pp. 999-1005, 1996, https://doi.org/10.1007/BF00242194.
- Z. Yan, G. Li, J. Wang, Z. Zhang, Z. Feng, M. Tang, and R. Zhang, “Electro-catalytic study of IrO2Ta2O5 coated anodes with pretreated titanium substrates,” Journal of Alloys and Compounds, vol. 680, pp. 60-66, 2016, https://doi.org/10.1016/j.jallcom.2016.04.090.
- Y. L. Xin, L. K. Xu, J. Wang, and X. Li, "Effect of sintering temperature on microstructure and electrocatalytic properties of Ti/IrO2-Ta2O5 anodes by pechini method," Rare Metal Materials and Engineering, vol. 39, no. 11, pp. 1903-1907, 2010, https://doi.org/10.1016/S1875-5372(10)60135-X.
- Z. Yan and H. Meng, "Effect of different shapes of the titanium-based IrO2-Ta2O5 coatings anode on electrochemical properties," Rare Metal Materials and Engineering, vol. 41, no. 5, pp. 772-775, 2012, https://doi.org/10.1016/S1875-5372(12)60047-2.
- P. C. S. Hayfield, "Development of the noble metal/oxide coated titanium electrode. Part III: Coated titanium anodes in widely ranging oxygen-evolving situations," Platinum Metals Review, vol. 42, no. 3, pp. 116-122, 1998, https://doi.org/10.1595/003214098X423116122.
- W. Monzel, A. P. Druschitz, and M. Maxfield, "Development of new, low-voltage, aluminum, sacrificial anode chemistries," In NACE CORROSION, pp. NACE-2014, 2014, https://onepetro.org/NACECORR/proceedings-abstract/CORR14/All-CORR14/123113.
- M. A. Li, H. J. Zeng, Y. G. Yan, and J. H. Qian, "Effects of Ga content on electrochemical properties of Al-Ga sacrificial anodes," Corrosion Science and Protection Technology, vol. 21, no. 2, pp. 125-127, 2009, https://www.cspt.org.cn/EN/Y2009/V21/I2/125.
- M. A. Li, W. L. Li, H. J. Zeng, Y. G. Yan, and B. R. Hou, "Low driving voltage Al-Ga sacrificial anode and its activation mechanism," Journal of Chinese Society for Corrosion and Protection, vol. 30, no. 4, pp. 329-332, 2010, https://www.jcscp.org/EN/Y2010/V30/I4/329.
- D. R. Sadoway, “Inert anodes for the Hall-Heroult cell: the ultimate materials challenge,” Jom, vol. 53, pp. 34-35, 2001, https://doi.org/10.1007/s11837-001-0206-5.
- I. Shtepliuk, V. Khranovskyy, G. Lashkarev, V. Khomyak, A. Ievtushenko, V. Tkach, V. Lazorenko, I. Timofeeva, and R. Yakimova, "Microstructure and luminescence dynamics of ZnCdO films with high Cd content deposited on different substrates by DC magnetron sputtering method," Applied Surface Science, vol. 276, pp. 550-557, 2013, https://doi.org/10.1016/j.apsusc.2013.03.132.
- G. Genchi, M. Sinicropi, G. Lauria, A. Carocci, and A. Catalano, "The effects of cadmium toxicity," International Journal of Environmental Research and Public Health, vol. 17, 2020, https://doi.org/10.3390/ijerph17113782.
- X. Zhang, C. Du, Z. Liu, and K. Liu, “The influence of temperature and dissolved oxygen on the electrochemical properties of three Al-Zn-In series sacrificial anodes,” International Journal of Electrochemical Science, vol. 16, no. 4, p. 210430, 2021, https://doi.org/10.20964/2021.04.02.
- J. Calderón, J. Barragán, J. Fierro, H. Mejía, C. González, V. Vázquez, K. Sánchez, M. Torres-Mancera, R. Retes-Mantilla, and R. Rodriguez-Diaz, "Corrosion Behavior of Al Modified with Zn in Chloride Solution," Materials, vol. 15, 2022, https://doi.org/10.3390/ma15124229.
- G. Sperandio, C. Santos, and A. Galdino, "Influence of silicon on the corrosion behavior of Al–Zn–In sacrificial anode," Journal of Materials Research and Technology, vol. 15, pp. 614-622, 2021, https://doi.org/10.1016/j.jmrt.2021.08.033.
- C. Rousseau, F. Baraud, L. Leleyter, and O. Gil, "Cathodic protection by zinc sacrificial anodes: Impact on marine sediment metallic contamination," Journal of Hazardous Materials, vol. 167, no. 1-3, pp. 953-958, 2009, https://doi.org/10.1016/j.jhazmat.2009.01.083.
- A. Jelmert and J. H. van Leeuwen, "Harming local species or preventing the transfer of exotics? Possible negative and positive effects of using zinc anodes for corrosion protection of ballast water tanks," Water Research, vol. 34, no. 6, pp. 1937-1940, 2000, https://doi.org/10.1016/S0043-1354(99)00416-9.
- J. Li, Z. Chen, J. Jing, and J. Hou, "Electrochemical behavior of Mg-Al-Zn-Ga-In alloy as the anode for seawater-activated battery," Journal of Materials Science & Technology, vol. 41, pp. 33-42, 2020, https://doi.org/10.1016/j.jmst.2019.08.052.
- Y. B. Huang, G. W. Song, H. D. Ding, X. B. Liu, and X. H. Shao, "Cathodic Protection Performance of Al-Zn-In-Mg-Ga-Mn Sacrificial Anode," Advanced Materials Research, vol. 214, pp. 296-300, 2011, https://doi.org/10.4028/www.scientific.net/AMR.214.296.
- H. S. Aljibori, A. Alamiery, and A. A. H. Kadhum, "Advances in corrosion protection coatings: A comprehensive review," International Journal of Corrosion and Scale Inhibition, vol. 12, no. 4, pp. 1476-1520, 2023, https://doi.org/10.17675/2305-6894-2023-12-4-6.
- P. C. S. Hayfield, "Platinised Titanium Electrodes for Cathodic Protection: Extensive use has Provided New Insights into the Electrochemical Properties of Platinum," Platinum Metals Review, vol. 27, no. 1, pp. 2-8, 1983, https://doi.org/10.1595/003214083X27128.
- P. C. S. Hayfield, "Development of the noble metal/oxide coated titanium electrode," Platinum Metals Review, vol. 42, no. 2, pp. 46-55, 1998, https://doi.org/10.1595/003214098X4224655.
- U. Eduok, J. Szpunar, and E. Ebenso, "Synthesis and characterization of anticorrosion zirconia/acrylic nanocomposite resin coatings for steel," Progress in Organic Coatings, vol. 137, p. 105337, 2019, https://doi.org/10.1016/j.porgcoat.2019.105337.
- M. R. Derakhshandeh, M. J. Eshraghi, and M. Razavi, "Recent developments in the new generation of hard coatings applied on cemented carbide cutting tools," International Journal of Refractory Metals and Hard Materials, vol. 111, p. 106077, 2023, https://doi.org/10.1016/j.ijrmhm.2022.106077.
- Y. X. Wang and S. Zhang, "Toward hard yet tough ceramic coatings," Surface and Coatings Technology, vol. 258, pp. 1-16, 2014, https://doi.org/10.1016/j.surfcoat.2014.07.007.
- A. Raza, S. Abdulahad, B. Kang, H. J. Ryu, and S. H. Hong, "Corrosion resistance of weight reduced AlxCrFeMoV high entropy alloys," Applied Surface Science, vol. 485, pp. 368-374, 2019, https://doi.org/10.1016/j.apsusc.2019.03.173.
- Y. Fu, J. Li, H. Luo, C. Du, and X. Li, "Recent advances on environmental corrosion behavior and mechanism of high-entropy alloys," Journal of Materials Science & Technology, vol. 80, pp. 217-233, 2021, https://doi.org/10.1016/j.jmst.2020.11.044.
- A. R. Khan, H.-J. Zhang, Z. Jun, S. M. Eldin, N. S. Alsaiari, and K. M. Katubi, "Electrochemical corrosion resistance of aluminum alloy 6101 with cerium-based coatings in an alkaline environment," Frontiers in Chemistry, vol. 10, p. 1066958, 2022, https://doi.org/10.3389/fchem.2022.1066958.
- S. M. Gad, S. Emad, X. Zhou, S. B. Lyon, Z. Jin, and I. M. Dagwa, "Effectiveness of strontium zinc phosphosilicate on the corrosion protection of AA2198-T851 aluminum alloy in sodium chloride solution," Corrosion Science, vol. 209, p. 110725, 2022, https://doi.org/10.1016/j.corsci.2022.110725.
- M. Ramezani, Z. M. Ripin, T. Pasang, and C.-P. Jiang, "Surface Engineering of Metals: Techniques, Characterizations and Applications," Metals, vol. 13, no. 7, p. 1299, 2023, https://doi.org/10.3390/met13071299.
- M. Liang, Y. Yuan, X. Li, J. Cheng, X. Zhang, K. Zhang, and R. You, "Enhanced corrosion resistance of Mg and Mg alloys with fs-laser printed hydrophobic and periodically microrippled surface for armor application," Applied Surface Science, vol. 639, p. 158156, 2023, https://doi.org/10.1016/j.apsusc.2023.158156.
- W. Yan, Y. Zhao, Y. Zhang, Q. Li, S. Chen, H. Yuan, Z. Zhang, L. Chen, J. Luo, P. Pang, G. He, M. Ying, and B. Liao, "Corrosion-resistant and interfacial conductive AlTiVCrMo high-entropy alloy and (AlTiVCrMo)Nx high-entropy ceramics coatings for surface modification of bipolar plates in proton exchange membrane fuel cells," Journal of Power Sources, vol. 527, p. 231217, 2022, https://doi.org/10.1016/j.jpowsour.2022.231217.
- W. Wu, Z. Huang, and T. Lim, "Recent development of mixed metal oxide anodes for electrochemical oxidation of organic pollutants in water," Applied Catalysis A: General, vol. 480, pp. 58-78, 2014, https://doi.org/10.1016/j.apcata.2014.04.035.
- L. Shao, P. He, J. Xue, and G. Li, "Electrolytic degradation of biorefractory organics and ammonia in leachate from bioreactor landfill," Water Science and Technology, vol. 53, no. 11, pp. 143-150, 2006, https://doi.org/10.2166/wst.2006.347.
- C. Tan, B. Xiang, Y. Li, J. Fang, and M. Huang, "Preparation and characteristics of a nano-PbO2 anode for organic wastewater treatment," Chemical Engineering Journal, vol. 166, no. 1, pp. 15-21, 2011, https://doi.org/10.1016/j.cej.2010.08.018.
- K. Pan, M. Tian, Z. H. Jiang, B. Kjartanson, and A. Chen, "Electrochemical oxidation of lignin at lead dioxide nanoparticles photoelectrodeposited on TiO2 nanotube arrays," Electrochimica Acta, vol. 60, pp. 147, 2012, https://doi.org/10.1016/j.electacta.2011.11.025.
- S. Li, F. Wang, M. Xu, Y. Wang, W. Fang, and Y. Hu, "Fabrication and characteristics of a nanostructure PbO2 anode and its application for degradation of phenol," Journal of The Electrochemical Society, vol. 160, no. 4, p. E44, 2013, https://doi.org/10.1149/2.082304jes.
- X. Meng, J. Yao, F. Liu, H. He, M. Zhou, P. Xiao, and Y. Zhang, "Preparation of SnO2@ C-doping TiO2 nanotube arrays and its electrochemical and photoelectrochemical properties," Journal of Alloys and Compounds, vol. 552, pp. 392-397, 2013, https://doi.org/10.1016/j.jallcom.2012.10.177.
- Y. Chen, L. Hong, H. Xue, W. Han, L. Wang, X. Sun, and J. Li, "Preparation and characterization of TiO2-NTs/SnO2-Sb electrodes by electrodeposition," Journal of Electroanalytical Chemistry, vol. 648, no. 2, pp. 119-127, 2010, https://doi.org/10.1016/j.jelechem.2010.08.004.
- Zhao, G., Cui, X., Liu, M., Li, P., Zhang, Y., Cao, T., and Li, D., "Electrochemical degradation of refractory pollutant using a novel microstructured TiO2 nanotubes/Sb-doped SnO2 electrode," Environmental Science & Technology, vol. 43, no. 5, pp. 1480-1486, 2009, https://doi.org/10.1021/es802155p.
- Pan, J. H., Chai, S. Y., Lee, C., Park, S. E., and Lee, W. I., "Controlled formation of highly crystallized cubic and hexagonal mesoporous SnO2 thin films," The Journal of Physical Chemistry C, vol. 111, no. 15, pp. 5582-5587, 2007, https://doi.org/10.1021/jp065529i.
- C. Weidmann, K. Brezesinski, C. Suchomski, K. Tropp, N. Grosser, J. Haetge, and T. Brezesinski, "Morphology-controlled synthesis of nanocrystalline η-Al2O3 thin films, powders, microbeads, and nanofibers with tunable pore sizes from preformed oligomeric oxo-hydroxo building blocks," Chemistry of Materials, vol. 24, no. 3, pp. 486-494, 2012, https://doi.org/10.1021/jp065529i.
- S. Chai, et al., "Novel sieve-like SnO2/TiO2 nanotubes with integrated photoelectrocatalysis: fabrication and application for efficient toxicity elimination of nitrophenol wastewater," The Journal of Physical Chemistry C, vol. 115, no. 37, pp. 18261-18269, 2011, https://doi.org/10.1021/jp205228h.
- Y. Wang et al., "Design of a novel Cu2O/TiO2/carbon aerogel electrode and its efficient electrosorption-assisted visible light photocatalytic degradation of 2, 4, 6-trichlorophenol," ACS Applied Materials & Interfaces, vol. 4, no. 8, pp. 3965-3972, 2012, https://doi.org/10.1021/am300795w.
- M. Wu, Y. Jin, G. Zhao, M. Li, and D. Li, "Electrosorption-promoted photodegradation of opaque wastewater on a novel TiO2/carbon aerogel electrode," Environmental Science & Technology, vol. 44, no. 5, pp. 1780-1785, 2010, https://doi.org/10.1021/es903201m.
- L. Frolova, N. Lyskov, and Y. Dobrovolsky, "Nanostructured Pt/SnO2–SbOx–RuO2 electrocatalysts for direct alcohol fuel cells," Solid State Ionics, vol. 225, pp. 92-98, 2012, https://doi.org/10.1016/j.ssi.2012.02.013.
- Y. Lee et al., "Highly single crystalline Ir x Ru1–x O2 mixed metal oxide nanowires," The Journal of Physical Chemistry C, vol. 116, no. 30, pp. 16300-16304, 2012, https://doi.org/10.1021/jp3048532.
- Y. Lee, H. Y. Shin, S. H. Chun, J. Lee, W. J. Park, J. M. Baik, et al., "Highly Single Crystalline Ir x Ru1–x O2 Mixed Metal Oxide Nanowires," J. Phys. Chem. C, vol. 116, no. 30, pp. 16300–16304, 2012, https://doi.org/10.1021/jp3048532.
- X. Cui, G. Zhu, Y. Pan, Q. Shao, M. Dong, Y. Zhang, and Z. Guo, "Polydimethylsiloxane-titania nanocomposite coating: fabrication and corrosion resistance," Polymer, vol. 138, pp. 203–210, 2018, https://doi.org/10.1016/j.polymer.2018.01.063.
- S. V. Harb, M. C. Uvida, A. Trentin, A. O. Lobo, T. J. Webster, S. H. Pulcinelli, et al., "PMMA-silica nanocomposite coating: Effective corrosion protection and biocompatibility for a Ti6Al4V alloy," Mater. Sci. Eng. C, vol. 110, p. 110713, 2020, https://doi.org/10.1016/j.msec.2020.110713.
- S. John, A. Salam, A. M. Baby, and A. Joseph, "Corrosion inhibition of mild steel using chitosan/TiO2 nanocomposite coatings," Prog. Org. Coat., vol. 129, pp. 254–259, 2019, https://doi.org/10.1016/j.porgcoat.2019.01.025.
- A. Chandra, L. S. Turng, P. Gopalan, R. M. Rowell, and S. Gong, "Study of utilizing thin polymer surface coating on the nanoparticles for melt compounding of polycarbonate/alumina nanocomposites and their optical properties," Compos. Sci. Technol., vol. 68, no. 3-4, pp. 768–776, 2008, https://doi.org/10.1016/j.compscitech.2007.08.027.
- J. Loste, J. M. Lopez-Cuesta, L. Billon, H. Garay, and M. Save, "Transparent polymer nanocomposites: An overview on their synthesis and advanced properties," Prog. Polym. Sci., vol. 89, pp. 133–158, 2019, https://doi.org/10.1016/j.progpolymsci.2018.10.003.
- X. Shi, T. A. Nguyen, Z. Suo, Y. Liu, and R. Avci, "Effect of nanoparticles on the anticorrosion and mechanical properties of epoxy coating," Surf. Coat. Technol., vol. 204, no. 3, pp. 237–245, 2009, https://doi.org/10.1016/j.surfcoat.2009.06.048.
- T. C. Huang, Y. A. Su, T. C. Yeh, H. Y. Huang, C. P. Wu, K. Y. Huang, et al., "Advanced anticorrosive coatings prepared from electroactive epoxy–SiO2 hybrid nanocomposite materials," Electrochim. Acta, vol. 56, no. 17, pp. 6142–6149, 2011, https://doi.org/10.1016/j.electacta.2011.04.053.
- S. Palraj, M. Selvaraj, K. Maruthan, and G. Rajagopal, "Corrosion and wear resistance behavior of nano-silica epoxy composite coatings," Prog. Org. Coat., vol. 81, pp. 132–139, 2015, https://doi.org/10.1016/j.porgcoat.2015.01.005.
- A. Ghanbari and M. M. Attar, "A study on the anticorrosion performance of epoxy nanocomposite coatings containing epoxy-silane treated nano-silica on mild steel substrate," J. Ind. Eng. Chem., vol. 23, pp. 145–153, 2015, https://doi.org/10.1016/j.jiec.2014.08.008.
- S. Ammar, K. Ramesh, B. Vengadaesvaran, S. Ramesh, and A. K. Arof, "A novel coating material that uses nano-sized SiO2 particles to intensify hydrophobicity and corrosion protection properties," Electrochim. Acta, vol. 220, pp. 417–426, 2016, https://doi.org/10.1016/j.electacta.2016.10.099.
- E. Barna, B. Bommer, J. Kürsteiner, A. Vital, O. V. Trzebiatowski, W. Koch, et al., "Innovative, scratch proof nanocomposites for clear coatings," Compos. Part A Appl. Sci. Manuf., vol. 36, no. 4, pp. 473–480, 2005, https://doi.org/10.1016/j.compositesa.2004.10.014.
- M. Yeganeh and A. Keyvani, "The effect of mesoporous silica nanocontainers incorporation on the corrosion behavior of scratched polymer coatings," Prog. Org. Coat., vol. 90, pp. 296–303, 2016, https://doi.org/10.1016/j.porgcoat.2015.11.006.
- M. Yeganeh and M. Saremi, "Corrosion inhibition of magnesium using biocompatible Alkyd coatings incorporated by mesoporous silica nanocontainers," Prog. Org. Coat., vol. 79, pp. 25–30, 2015, https://doi.org/10.1016/j.porgcoat.2014.10.015.
- J. F. Pagotto, F. J. Recio, A. D. J. Motheo, and P. Herrasti, "Multilayers of PAni/n-TiO2 and PAni on carbon steel and welded carbon steel for corrosion protection," Surf. Coat. Technol., vol. 289, pp. 23–28, 2016, https://doi.org/10.1016/j.surfcoat.2016.01.046.
- N. Wang, W. Fu, J. Zhang, X. Li, and Q. Fang, "Corrosion performance of waterborne epoxy coatings containing polyethylenimine treated mesoporous-TiO2 nanoparticles on mild steel," Prog. Org. Coat., vol. 89, pp. 114–122, 2015, https://doi.org/10.1016/j.porgcoat.2015.07.009.
- S. Radhakrishnan, C. R. Siju, D. Mahanta, S. Patil, and G. Madras, "Conducting polyaniline–nano-TiO2 composites for smart corrosion resistant coatings," Electrochim. Acta, vol. 54, no. 4, pp. 1249–1254, 2009, https://doi.org/10.1016/j.electacta.2008.08.069.
- A. Mostafaei and F. Nasirpouri, "Epoxy/polyaniline–ZnO nanorods hybrid nanocomposite coatings: Synthesis, characterization and corrosion protection performance of conducting paints," Prog. Org. Coat., vol. 77, no. 1, pp. 146–159, 2014, https://doi.org/10.1016/j.porgcoat.2013.08.015.
- A. Olad and R. Nosrati, "Preparation and corrosion resistance of nanostructured PVC/ZnO–polyaniline hybrid coating," Prog. Org. Coat., vol. 76, no. 1, pp. 113–118, 2013, https://doi.org/10.1016/j.porgcoat.2013.08.015.
- N. Elangovan, A. Srinivasan, S. Pugalmani, N. Rajendiran, and N. Rajendran, "Development of poly (vinylcarbazole)/alumina nanocomposite coatings for corrosion protection of 316L stainless steel in 3.5% NaCl medium," J. Appl. Polym. Sci., vol. 134, no. 27, p. 44937, 2017, https://doi.org/10.1002/app.44937.
- S. Khasim, S. C. Raghavendra, M. Revanasiddappa, K. C. Sajjan, M. Lakshmi, and M. Faisal, "Synthesis, characterization and magnetic properties of polyaniline/γ-Fe 2 O 3 composites," Bull. Mater. Sci., vol. 34, pp. 1557–1561, 2011, https://doi.org/10.1007/s12034-011-0358-z.
- L. S. Živković, J. P. Popić, B. V. Jegdić, Z. Dohčević-Mitrović, J. B. Bajat, and V. B. Mišković-Stanković, "Corrosion study of ceria coatings on AA6060 aluminum alloy obtained by cathodic electrodeposition: effect of deposition potential," Surf. Coat. Technol., vol. 240, pp. 327–335, 2014, https://doi.org/10.1016/j.surfcoat.2013.12.048.
- M. A. Arenas, A. Conde, and J. J. De Damborenea, "Cerium: a suitable green corrosion inhibitor for tinplate," Corros. Sci., vol. 44, no. 3, pp. 511–520, 2002, https://doi.org/10.1016/S0010-938X(01)00053-1.
- S. A. Umoren and A. Madhankumar, "Effect of addition of CeO2 nanoparticles to pectin as inhibitor of X60 steel corrosion in strong acid media: synergistic and mechanistic implications," J. Adhes. Sci. Technol., vol. 30, no. 13, pp. 1424–1443, 2016, https://doi.org/10.1016/j.molliq.2016.09.082.
- M. F. Smiechowski and V. F. Lvovich, "Characterization of non-aqueous dispersions of carbon black nanoparticles by electrochemical impedance spectroscopy," J. Electroanal. Chem., vol. 577, no. 1, pp. 67–78, 2005, https://doi.org/10.1016/j.jelechem.2004.11.015.
- M. F. Smiechowski and V. F. Lvovich, "Characterization of non-aqueous dispersions of carbon black nanoparticles by electrochemical impedance spectroscopy," Journal of Electroanalytical Chemistry, vol. 577, no. 1, pp. 67-78, 2005, https://doi.org/10.1016/j.jelechem.2004.11.028.
- A. Ghasemi-Kahrizsangi, H. Shariatpanahi, J. Neshati, and E. Akbarinezhad, "Corrosion behavior of modified nano carbon black/epoxy coating in accelerated conditions," Applied Surface Science, vol. 331, pp. 115-126, 2015, https://doi.org/10.1016/j.apsusc.2015.01.008.
- A. Foyet, T. H. Wu, A. Kodentsov, L. G. J. van der Ven, and R. A. T. M. van Benthem, "Corrosion protection and delamination mechanism of epoxy/carbon black nanocomposite coating on AA2024-T3," Journal of The Electrochemical Society, vol. 160, no. 4, pp. C159-C167, 2013, https://doi.org/10.1149/2.063304jes.
- H. Wang et al., "Anisotropy in tribological performances of long aligned carbon nanotubes/polymer composites," Carbon, vol. 67, pp. 38-47, 2014, https://doi.org/10.1016/j.carbon.2013.09.032.
- B. Prasanna, D. Avadhani, M. Raghu, and Y. Kumar, "Studies on ZnS nanoparticles reinforced epoxy nanocomposites for corrosion resistance applications," Materials Today Communications, vol. 12, pp. 72-78, 2017, https://doi.org/10.1016/j.mtcomm.2017.03.004.
- V. D. Punetha et al., "Functionalization of carbon nanomaterials for advanced polymer nanocomposites: A comparison between CNT and graphene," Progress in Polymer Science, vol. 67, pp. 1-47, 2017, https://doi.org/10.1016/j.progpolymsci.2016.12.009.
- S. Pourhashem, M. R. Vaezi, A. Rashidi, and M. R. Bagherzadeh, "Exploring corrosion protection properties of solvent based epoxy-graphene oxide nanocomposite coatings on mild steel," Corrosion Science, vol. 115, pp. 78-92, 2017, https://doi.org/10.1016/j.corsci.2016.11.013.
- Y. Cui, S. I. Kundalwal, and S. Kumar, "Gas barrier performance of graphene/polymer nanocomposites," Carbon, vol. 98, pp. 313-333, 2016, https://doi.org/10.1016/j.carbon.2015.11.018.
- C. H. Chang et al., "Novel anticorrosion coatings prepared from polyaniline/graphene composites," Carbon, vol. 50, no. 14, pp. 5044-5051, 2012, https://doi.org/10.1016/j.carbon.2012.06.048.
- Q. Zhu et al., "Epoxy coating with in-situ synthesis of polypyrrole functionalized graphene oxide for enhanced anticorrosive performance," Progress in Organic Coatings, vol. 140, p. 105488, 2020, https://doi.org/10.1016/j.porgcoat.2019.105488.
- J. González-Guzmán, J. J. Santana, S. González, and R. M. Souto, "Resistance of metallic substrates protected by an organic coating containing glass flakes," Progress in Organic Coatings, vol. 68, no. 3, pp. 240-243, 2010, https://doi.org/10.1016/j.porgcoat.2010.01.007.
- S. Zuo et al., "Polyaniline/g-C3N4 composites as novel media for anticorrosion coatings," Journal of Coatings Technology and Research, vol. 14, pp. 1307-1314, 2017, https://doi.org/10.1007/s11998-017-9916-7.
- E. Husain et al., "Marine corrosion protective coatings of hexagonal boron nitride thin films on stainless steel," ACS Applied Materials & Interfaces, vol. 5, no. 10, pp. 4129-4135, 2013, https://doi.org/10.1021/am400016y.
- M. D. Sanchez-Garcia and J. M. Lagaron, "On the use of plant cellulose nanowhiskers to enhance the barrier properties of polylactic acid," Cellulose, vol. 17, pp. 987-1004, 2010, https://doi.org/10.1007/s10570-010-9430-x.
- A. M. Kumar et al., "Electrochemical and in vitro bioactivity of polypyrrole/ceramic nanocomposite coatings on 316L SS bio-implants," Materials Science and Engineering: C, vol. 43, pp. 76-85, 2014, https://doi.org/10.1016/j.msec.2014.06.023.
- M. A. Deyab, N. Hamdi, M. Lachkar, and B. El Bali, "Clay/Phosphate/Epoxy nanocomposites for enhanced coating activity towards corrosion resistance," Progress in Organic Coatings, vol. 123, pp. 232-237, 2018, https://doi.org/10.1016/j.porgcoat.2018.07.003.
- D. LeCorre et al., "All starch nanocomposite coating for barrier material," Journal of Applied Polymer Science, vol. 131, no. 3, 2014, https://doi.org/10.1002/app.39750.
- M. L. Zheludkevich et al., "Self-healing protective coatings with 'green' chitosan based pre-layer reservoir of corrosion inhibitor," Journal of Materials Chemistry, vol. 21, no. 13, pp. 4805-4812, 2011, https://doi.org/10.1039/c1jm10304k.
- U. Eduok and J. Szpunar, "Ultrasound-assisted synthesis of zinc molybdate nanocrystals and molybdate-doped epoxy/PDMS nanocomposite coatings for Mg alloy protection," Ultrasonics Sonochemistry, vol. 44, pp. 288-298, 2018, https://doi.org/10.1016/j.ultsonch.2018.02.019.
- M. H. Moradi, M. Aliofkhazraei, M. Toorani, A. Golgoon, and A. S. Rouhaghdam, "SiAlON–epoxy nanocomposite coatings: Corrosion and wear behavior," Journal of Applied Polymer Science, vol. 133, no. 35, 2016, https://doi.org/10.1002/app.43995.
- H. R. Bakhsheshi-Rad, E. Hamzah, M. Kasiri-Asgarani, S. Jabbarzare, N. Iqbal, and M. A. Kadir, "Deposition of nanostructured fluorine-doped hydroxyapatite–polycaprolactone duplex coating to enhance the mechanical properties and corrosion resistance of Mg alloy for biomedical applications," Mater. Sci. Eng. C, vol. 60, pp. 526–537, 2016, https://doi.org/10.1016/j.msec.2015.11.057.
- B. A. Bhanvase and S. H. Sonawane, "New approach for simultaneous enhancement of anticorrosive and mechanical properties of coatings: Application of water repellent nano CaCO3–PANI emulsion nanocomposite in alkyd resin," Chem. Eng. J., vol. 156, no. 1, pp. 177–183, 2010, https://doi.org/10.1016/j.cej.2009.10.013.
- S. M. Mousavifard, P. M. Nouri, M. M. Attar, and B. Ramezanzadeh, "The effects of zinc aluminum phosphate (ZPA) and zinc aluminum polyphosphate (ZAPP) mixtures on corrosion inhibition performance of epoxy/polyamide coating," J. Ind. Eng. Chem., vol. 19, no. 3, pp. 1031–1039, 2013, https://doi.org/10.1016/j.jiec.2012.11.027.
- W. G. Ji, J. M. Hu, L. Liu, J. Q. Zhang, and C. N. Cao, "Improving the corrosion performance of epoxy coatings by chemical modification with silane monomers," Surf. Coat. Technol., vol. 201, no. 8, pp. 4789–4795, 2007, https://doi.org/10.1016/j.surfcoat.2006.09.100.
- M. A. Deyab, A. De Riccardis, and G. Mele, "Novel epoxy/metal phthalocyanines nanocomposite coatings for corrosion protection of carbon steel," J. Mol. Liq., vol. 220, pp. 513–517, 2016, https://doi.org/10.1016/j.molliq.2016.04.115.
- S. Y. Arman, B. Ramezanzadeh, S. Farghadani, M. Mehdipour, and A. Rajabi, "Application of the electrochemical noise to investigate the corrosion resistance of an epoxy zinc-rich coating loaded with lamellar aluminum and micaceous iron oxide particles," Corros. Sci., vol. 77, pp. 118–127, 2013, https://doi.org/10.1016/j.corsci.2013.07.034.
- M. K. Madhup, N. K. Shah, and P. M. Wadhwani, "Investigation of surface morphology, anti-corrosive and abrasion resistance properties of nickel oxide epoxy nanocomposite (NiO-ENC) coating on mild steel substrate," Prog. Org. Coat., vol. 80, pp. 1–10, 2015, https://doi.org/10.1016/j.porgcoat.2014.11.007.
- H. Choi, Y. K. Song, K. Y. Kim, and J. M. Park, "Encapsulation of triethanolamine as organic corrosion inhibitor into nanoparticles and its active corrosion protection for steel sheets," Surf. Coat. Technol., vol. 206, no. 8–9, pp. 2354–2362, 2012, https://doi.org/10.1016/j.surfcoat.2011.10.030.
- B. Ramezanzadeh, G. Bahlakeh, and M. Ramezanzadeh, "Polyaniline-cerium oxide (PAni-CeO2) coated graphene oxide for enhancement of epoxy coating corrosion protection performance on mild steel," Corros. Sci., vol. 137, pp. 111–126, 2018, https://doi.org/10.1016/j.corsci.2018.03.038.
- Z. Yu, H. Di, Y. Ma, L. Lv, Y. Pan, C. Zhang, and Y. He, "Fabrication of graphene oxide–alumina hybrids to reinforce the anti-corrosion performance of composite epoxy coatings," Appl. Surf. Sci., vol. 351, pp. 986–996, 2015, https://doi.org/10.1016/j.apsusc.2015.06.026.
- Y. Zhan, J. Zhang, X. Wan, Z. Long, S. He, and Y. He, "Epoxy composites coating with Fe3O4 decorated graphene oxide: Modified bio-inspired surface chemistry, synergistic effect and improved anti-corrosion performance," Appl. Surf. Sci., vol. 436, pp. 756–767, 2018, https://doi.org/10.1016/j.apsusc.2017.12.095.
- M. G. Sari, M. Shamshiri, and B. Ramezanzadeh, "Fabricating an epoxy composite coating with enhanced corrosion resistance through impregnation of functionalized graphene oxide-co-montmorillonite Nanoplatelet," Corros. Sci., vol. 129, pp. 38–53, 2017, https://doi.org/10.1016/j.corsci.2017.09.024.
- M. Rui, Y. Jiang, and A. Zhu, "Sub-micron calcium carbonate as a template for the preparation of dendrite-like PANI/CNT nanocomposites and its corrosion protection properties," Chem. Eng. J., vol. 385, p. 123396, 2020, https://doi.org/10.1016/j.cej.2019.123396.
- D. E. Tallman, G. Spinks, A. Dominis, and G. G. Wallace, "Electroactive conducting polymers for corrosion control," J. Solid State Electrochem., vol. 6, pp. 73–84, 2002, https://doi.org/10.1007/s100080100212.
- E. Armelin, Á. Meneguzzi, C. A. Ferreira, and C. Alemán, "Conducting polymers in organic coatings," Surf. Coat. Technol., vol. 203, pp. 3763–3769, 2009, https://doi.org/10.1016/j.surfcoat.2009.06.019.
- P. Chandrasekhar. Conducting Polymers, Fundamentals and Applications: A Practical Approach. New York, NY: Springer. 1999. https://doi.org/10.1007/978-1-4615-5245-1.
- G. Inzelt. Conducting Polymers: A New Era in Electrochemistry. New York, NY: Springer. 2012. https://doi.org/10.1007/978-3-642-27621-7.
- K. Saravanan, S. Sathiyanarayanan, S. Muralidharan, S. S. Azim, and G. Venkatachari, "Performance evaluation of polyaniline pigmented epoxy coating for corrosion protection of steel in concrete environment," Prog. Org. Coat., vol. 59, no. 2, pp. 160–167, 2007, https://doi.org/10.1016/j.porgcoat.2007.03.002.
- M. A. S. Oliveira, J. J. Moraes, and R. Faez, "Impedance studies of poly(methylmethacrylate-co-acrylic acid) doped polyaniline films on aluminum alloy," Prog. Org. Coat., vol. 65, no. 3, pp. 348–356, 2009, https://doi.org/10.1016/j.porgcoat.2009.02.003.
- A. J. Dominis, G. M. Spinks, and G. G. Wallace, "Comparison of polyaniline primers prepared with different dopants for corrosion protection of steel," Prog. Org. Coat., vol. 48, no. 1, pp. 43–49, 2003, https://doi.org/10.1016/S0300-9440(03)00111-5.
- K. Kamaraj, S. Sathiyanarayanan, S. Muthukrishnan, and G. Venkatachari, "Corrosion Protection of Iron by Benzoate Doped Polyaniline Containing Coatings," Progress in Organic Coatings, vol. 64, no. 4, pp. 460-465, 2009, https://doi.org/10.1016/j.porgcoat.2008.11.005.
- S. Shimizu, T. Saitoh, M. Uzawa, M. Yuasa, K. Yano, T. Maruyama, and K. Watanabe, "Synthesis and Applications of Sulfonated Polyaniline," Synthetic Metals, vol. 85, no. 1-3, pp. 1337-1338, 1997, https://doi.org/10.1016/S0379-6779(97)80260-3.
- Y. Sahin, K. Pekmez, and A. Yildiz, "Electrochemical Preparation of Soluble Sulfonated Polymers and Aniline Copolymers of Aniline Sulfonic Acids in Dimethylsulfoxide," Journal of Applied Polymer Science, vol. 90, no. 8, pp. 2163-2169, 2003, https://doi.org/10.1002/app.12741.
- C.-W. Peng et al., "Nanocasting Technique to Prepare Polyaniline Surface with Biomimetic Superhydrophobic Structures for Anticorrosion Application," Electrochimica Acta, vol. 95, pp. 192-199, 2013, https://doi.org/10.1016/j.electacta.2013.01.070.
- E. Armelin et al., "Corrosion Protection with Polyaniline and Polypyrrole as Anticorrosive Additives for Epoxy Paint," Corrosion Science, vol. 50, no. 3, pp. 721-728, 2008, https://doi.org/10.1016/j.corsci.2007.10.006.
- D. Kowalski, M. Ueda, and T. Ohtsuka, "Corrosion Protection of Steel by Bi-layered Polypyrrole Doped with Molybdophosphate and Naphthalenedisulfonate Anions," Corrosion Science, vol. 49, no. 3, pp. 1635-1644, 2007, https://doi.org/10.1016/j.corsci.2006.08.018.
- G. Bereket and E. Hür, "The Corrosion Protection of Mild Steel by Single Layered Polypyrrole and Multilayered Polypyrrole/Poly(5-amino-1-naphthol) Coatings," Progress in Organic Coatings, vol. 65, no. 1, pp. 116-124, 2009, https://doi.org/10.1016/j.porgcoat.2008.08.006.
- P. Herrasti, A. I. del Rio, and J. Recio, "Electrodeposition of Homogeneous and Adherent Polypyrrole on Copper for Corrosion Protection," Electrochimica Acta, vol. 52, no. 23, pp. 6496-6501, 2007, https://doi.org/10.1016/j.electacta.2007.04.083.
- Y. F. Jiang, X. W. Guo, Y. H. Wei, C. Q. Zhai, and W. J. Ding, "Corrosion Protection of Polypyrrole Electrodeposited on AZ91 Magnesium Alloys in Alkaline Solutions," Synthetic Metals, vol. 139, no. 2, pp. 335-339, 2003, https://doi.org/10.1016/S0379-6779(03)00181-4.
- N. Attarzadeh, K. Raeissi, and M. A. Golozar, "Effect of Saccharin Addition on the Corrosion Resistance of Polypyrrole Coatings," Progress in Organic Coatings, vol. 63, no. 2, pp. 167-174, 2008, https://doi.org/10.1016/j.porgcoat.2008.03.003.
- M. G. Hosseini, M. Raghibi-Boroujeni, I. Ahadzadeh, R. Najjar, and M. S. Seyed Dorraji, "Effect of Polypyrrole-Montmorillonite Nanocomposites Powder Addition on Corrosion Performance of Epoxy Coatings on Al 5000," Progress in Organic Coatings, vol. 66, no. 3, pp. 321-327, 2009, https://doi.org/10.1016/j.porgcoat.2009.06.011.
- D. E. Tallman et al., "Nanocomposite of Polypyrrole and Alumina Nanoparticles as a Coating Filler for the Corrosion Protection of Aluminum Alloy 2024-T3," Applied Surface Science, vol. 254, no. 17, pp. 5452-5459, 2008, https://doi.org/10.1016/j.apsusc.2008.02.127.
- G. Kousik, S. Pitchumani, and N. G. Renganathan, "Electrochemical Characterization of Polythiophene-Coated Steel," Progress in Organic Coatings, vol. 43, no. 4, pp. 286-291, 2001, https://doi.org/10.1016/S0300-9440(01)00211-9.
- C. Ocampo et al., "Application of a Polythiophene Derivative as Anticorrosive Additive for Paints," Progress in Organic Coatings, vol. 53, no. 3, pp. 217-224, 2005, https://doi.org/10.1016/j.porgcoat.2005.01.006.
- U. Rammelt, P. T. Nguyen, and W. Plieth, "Protection of Mild Steel by Modification with Thin Films of Polymethylthiophene," Electrochimica Acta, vol. 46, no. 26-27, pp. 4251-4257, 2001, https://doi.org/10.1016/S0013-4686(01)00688-0.
- M. Rohwerder and A. Michalik, "Conducting Polymers for Corrosion Protection: What Makes the Difference Between Failure and Success?" Electrochimica Acta, vol. 53, no. 3, pp. 1300-1313, 2007, https://doi.org/10.1016/j.electacta.2007.05.026.
- B. N. Grgur, M. M. Gvozdenović, V. B. Mišković-Stanković, and Z. Kačarević-Popović, "Corrosion Behavior and Thermal Stability of Electrodeposited PANI/epoxy Coating System on Mild Steel in Sodium Chloride Solution," Progress in Organic Coatings, vol. 56, no. 2-3, pp. 214-219, 2006, https://doi.org/10.1016/j.porgcoat.2006.05.003.
- G. Williams, R. J. Holness, D. A. Worsley, and H. N. McMurray, "Inhibition of Corrosion-Driven Organic Coating Delamination on Zinc by Polyaniline," Electrochemistry Communications, vol. 6, no. 6, pp. 549-555, 2004, https://doi.org/10.1016/j.elecom.2004.04.004.
- E. Armelin et al., "Corrosion Protection with Polyaniline and Polypyrrole as Anticorrosive Additives for Epoxy Paint," Corrosion Science, vol. 50, no. 3, pp. 721-728, 2008, https://doi.org/10.1016/j.corsci.2007.10.006.
- P. Hayfield and A. Hill, "Anwendung der Diskreten Ebonex Anoden für den Kathodischen Schutz der Bewehrung an Beton: Das Verhalten des Ebofix Mörtels / Ebonex® Discrete Anodes in the Cathodic Protection of Rebar in Concrete: Performance of Ebofix Grouts," Restoration of Buildings and Monuments, vol. 6, pp. 647-654, 2000, https://doi.org/10.1515/rbm-2000-5516.
- D. Ainakulova et al., "Analytical Review of Conductive Coatings, Cathodic Protection, and Concrete," Kompleksnoe Ispolʹzovanie Mineralʹnogo syrʹâ / Complex Use of Mineral Resources / Mineraldik Shikisattardy Keshendi Paidalanu, vol. 329, no. 2, pp. 92-102, 2023, https://doi.org/10.31643/2024/6445.20.
- T. Pietrzak, M. Wasiucionek, and J. Garbarczyk, "Towards Higher Electric Conductivity and Wider Phase Stability Range via Nanostructured Glass-Ceramics Processing," Nanomaterials, vol. 11, 2021, https://doi.org/10.3390/nano11051321.
- H. Abbasi, K. Jafarzadeh, and S. Mirali, "An investigation of the effect of RuO2 on the deactivation and corrosion mechanism of a Ti/IrO2 + Ta2O5 coating in an OER application," J. Electroanal. Chem., vol. 777, pp. 67-74, 2016, https://doi.org/10.1016/j.jelechem.2016.07.036.
- F. Wu, J. Bai, J. Feng, and S. Xiong, "Porous mixed metal oxides: design, formation mechanism, and application in lithium-ion batteries," Nanoscale, vol. 7, no. 41, pp. 17211-30, 2015, https://doi.org/10.1039/C5NR04791A.
- G. Chang et al., "Dynamic Reconstructed RuO2/NiFeOOH with Coherent Interface for Efficient Seawater Oxidation," Small, vol. 19, no. 12, p. e2206768, 2023, https://doi.org/10.1002/smll.202206768.
- W. Jurczak, "Passive Corrosion Protection of Al-Zn-Mg alloy in Seawater," Naše More, vol. 66, no. 3, pp. 157-161, 2019, https://doi.org/10.17818/NM/2019/3.2.
- K. Du et al., "Durability of platinum coating anode in molten carbonate electrolysis cell," Corros. Sci., vol. 154, pp. 125-135, 2019, https://doi.org/10.1016/j.corsci.2019.03.028.
- A. Korczyński, A. Doniec, and J. Świderski, "Studies on the durability of platinum and ruthenium oxide coated titanium anodes in the d-ribono-γ-lactone electro-reduction process," Corros. Sci., vol. 21, no. 5, pp. 329-332, 1981, https://doi.org/10.1016/0010-938X(81)90070-6.
- S. Yu, S. Lee, D. Lee, Y. Sung, and T. Hyeon, "Conversion Reaction-Based Oxide Nanomaterials for Lithium Ion Battery Anodes," Small, vol. 12, no. 16, pp. 2146-2172, 2016, https://doi.org/10.1002/smll.201502299.
- C. Casas and W. Li, "A review of application of carbon nanotubes for lithium ion battery anode material," J. Power Sources, vol. 208, pp. 74-85, 2012, https://doi.org/10.1016/j.jpowsour.2012.02.013.
- C. Tan and D. Blackwood, "Corrosion protection by multilayered conducting polymer coatings," Corros. Sci., vol. 45, no. 3, pp. 545-557, 2003, https://doi.org/10.1016/S0010-938X(02)00144-0.
- F. Gao, J. Mu, Z. Bi, S. Wang, and Z. Li, "Recent advances of polyaniline composites in anticorrosive coatings: A review," Prog. Org. Coat., vol. 151, p. 106071, 2021, https://doi.org/10.1016/j.porgcoat.2020.106071.
- J. Zuo, W. Yao, J. Xu, Y. Chen, and X. Liu, “Effects of Carbon Nanotube-Carbon Fiber Cementitious Conductive Anode for Cathodic Protection of Reinforced Concrete,” J. Test. Eval., vol. 45, no. 5, pp. 1777–1786, 2017, https://doi.org/10.1520/JTE20160062.
- A. Mostafaei and F. Nasirpouri, “Epoxy/polyaniline–ZnO nanorods hybrid nanocomposite coatings: Synthesis, characterization and corrosion protection performance of conducting paints,” Prog. Org. Coat., vol. 77, no. 1, pp. 146–159, 2014, https://doi.org/10.1016/j.porgcoat.2013.08.015.
- Y. Xu, W. Zhang, W. Yu, J. Ding, and H. Sun, “Polythiophene-sensitized TiO₂ nanotube arrays for photo-generated cathodic protection of 304 stainless steel,” J. Mater. Sci., vol. 56, pp. 4470–4483, 2021, https://doi.org/10.1007/s10853-020-05528-z.
- W. Li, J. Zuo, J. Xu, Y. Li, H. Zheng, and H. Yang, “Cathodic protection of reinforced concrete facilitated by using CNT-CF/cement-based auxiliary anode,” Fuller. Nanotub. Carbon Nanostruct., vol. 32, no. 6, pp. 595–602, 2024, https://doi.org/10.1080/1536383X.2024.2309936.
- J. Li et al., “Enhancing cathodic protection and barrier properties of zinc-rich epoxy coatings with mesoporous Ti₄O₇ additive,” Prog. Org. Coat., vol. 187, p. 108163, 2024, https://doi.org/10.1016/j.porgcoat.2023.108163.
- D. T. Oloruntoba, O. S. Adesina, O. O. Sanyaolu, P. P. Ikubanni, B. O. Iwarere, and A. A. Adediran, “Development of Aluminum Base Anode for Cathodic Protection of Steel,” Chem. Afr., pp. 1–14, 2024, https://doi.org/10.1007/s42250-024-00962-x.
- X. Zhou et al., “Low efficiency of cathodic protection in marine tidal corrosion of X80 steel in the presence of Pseudomonas sp.,” Bioelectrochemistry, vol. 157, p. 108656, 2024, https://doi.org/10.1016/j.bioelechem.2024.108656.
- A. B. Abdel-Aziz, F. E. T. Heakal, R. M. El Nashar, and I. M. Ghayad, “Green synthesis and characterization of binary, ternary, and quaternary Ti/MMO anodes for chlorine and oxygen evolution reactions,” Sci. Rep., vol. 14, no. 1, p. 9821, 2024, https://doi.org/10.1038/s41598-024-59595-2.
- M. A. Zavareh, A. A. D. M. Sarhan, R. Karimzadeh, R. Singh, and K. Singh, “Analysis of corrosion protection behavior of Al₂O₃-TiO₂ oxide ceramic coating on carbon steel pipes for the petroleum industry,” Ceram. Int., vol. 44, no. 6, pp. 5967–5975, 2018, https://doi.org/10.1016/j.ceramint.2017.12.175.
- A. U. Ammar et al., “Electrochemical study of polymer and ceramic-based nanocomposite coatings for corrosion protection of cast iron pipeline,” Mater., vol. 11, no. 3, p. 332, 2018, https://doi.org/10.3390/ma11030332.
- X. T. Wang et al., “CdTe/TiO₂ nanocomposite material for photogenerated cathodic protection of 304 stainless steels,” Mater. Sci. Eng. B, vol. 208, pp. 22–28, 2016, https://doi.org/10.1016/j.mseb.2016.02.006.
- S. Cui, X. Yin, Q. Yu, Y. Liu, D. Wang, and F. Zhou, “Polypyrrole nanowire/TiO₂ nanotube nanocomposites as photoanodes for photocathodic protection of Ti substrate and 304 stainless steel under visible light,” Corros. Sci., vol. 98, pp. 471-477, 2015, https://doi.org/10.1016/j.corsci.2015.05.059.
- H. Hayatdavoudi and M. Rahsepar, “A mechanistic study of the enhanced cathodic protection performance of graphene-reinforced zinc rich nanocomposite coating for corrosion protection of carbon steel substrate,” J. Alloy. Compd., vol. 727, pp. 1148-1156, 2017, https://doi.org/10.1016/j.jallcom.2017.08.250.
- Y. Cubides and H. Castaneda, “Corrosion protection mechanisms of carbon nanotube and zinc-rich epoxy primers on carbon steel in simulated concrete pore solutions in the presence of chloride ions,” Corros. Sci., vol. 109, pp. 145–161, 2016, https://doi.org/10.1016/j.corsci.2016.03.023.
- Y. Cubides and H. Castaneda, “Corrosion protection mechanisms of carbon nanotube and zinc-rich epoxy primers on carbon steel in simulated concrete pore solutions in the presence of chloride ions,” Corrosion Science, vol. 109, pp. 145-161, 2016, https://doi.org/10.1016/j.corsci.2016.03.023.
Advancements in Anode Materials for Cathodic Protection: Nanostructured Alloys, Surface Modifications, and Smart Monitoring (Madaniyyu Sulaiman Yahaya)